A People-Centric Approach to Digital Transformation – A 9 Plant Manufacturing Execution System (MES) Deployment Example
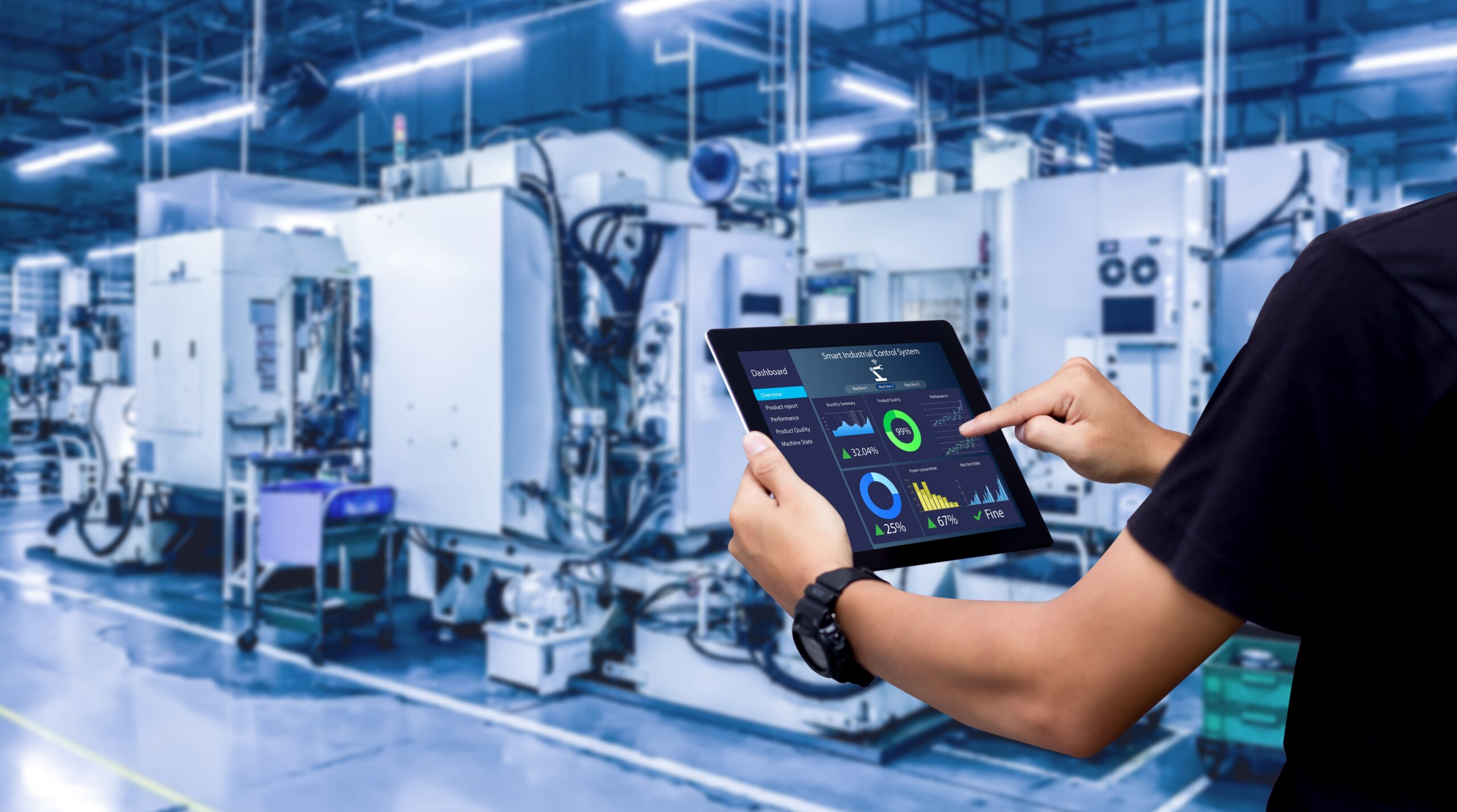
The AVEVA MES – Helix project started in 2017 with the plan to deploy the system in nine factories. Starting with the most challenging manufacturing sites, InSource Solutions set the standards and processes for the additional facilities with ease. The plants went from pencil and paper to Dashboards, Reports, and a Quality Cockpit.
In today’s dynamic environment, manufacturers must prioritize agility and resilience in the industry. Continuous Improvement Specialists have always understood the foundation for this. It is critical to the manufacturer’s success to empower their people and culture to consistently improve quality, efficiency, and profitability through data-driven decision-making. While continuing their digital transformation journey, it is imperative to effectively provide the correct data within the proper context to the right people at the right time. A good training process helps manufacturers—from the plant floor to management—feel confident in and empowered by the new systems and processes, ultimately leading to a better adoption rate. The AVEVA MES – Helix project shows how effective a good training program and the correct data to the right people can support a manufacturer and ensure their team is successful.
As part of the deployment strategy, the project team focused its efforts on the three most challenging factories and applied the final approach and learnings to the six additional manufacturing facilities. Starting with the most challenging factories, we utilized our six-week training course allowing us to implement this process in the other factories effectively. This training method helped the plant team learn hands-on the abilities AVEVA MES could accomplish for their shop floor. By the end of the training, all shop floor employees were running the MES Helix system like a well-oiled machine.
InSource ensures your team is well-trained and confident in the automation software we deploy. We work with you in your facility, in our classrooms, or online—both live and self-paced—to train and engage your workforce in your newest AVEVA software deployments. Here’s a snapshot of what an MES deployment with InSource might look like for your factory.
Week 1-3: Onsite Training and Support
InSource Solution’s onsite training consists of one-on-one training with the operators at their workstations. Our hands-on portion of the training consists of two 12-hour shifts covering Samples creation, Downtime, Quality, and Shift End Processes. All training is done at the employee’s pace of learning and conducted at their workstation, which ensures the trainee is comfortable and confident with the new system. A weekly report, along with the Coaching Matrix, is presented by tracking the supervisor’s adaptation. Week three is the Go-Live week, where Helix becomes the system for manufacturing. InSource can monitor and support the employees by going live in the hands-on portion to ensure a smooth transition.
Week 4-5: Support for Architect
After the first three weeks with our InSource Trainers, we move to the next part of the AVEVA MES deployment to the factory. In weeks four thru five, InSource gives control to the employees as all additional support for the Helix engagement goes away. InSource Trainers will then only support the transition of InSource System Architect. After the factory employees get accustomed to the System Architect, we move to the final stage of the deployment.
Week 6: System Health Check
The final stage of the deployment is conducting a health check that covers all aspects of the Helix engagement. The Helix Health Assessment consists of the following areas:
- Team Meetings: The supervisors use Dashboards for Shift Handoffs per production line instead of pencil and paper.
- Floor Engagements: Evaluating how supervisors and managers engage with the floor employees throughout the production shift using Helix Walks.
- Work Orders: Examining to see if all Work Orders are opened and closed correctly.
- Quality: Checking all quality samples are completed for each shift and are comments placed on Red sample results.
- Leadership: Are Leaders on the production floor interacting with employees and getting vital feedback from all?
- Reports: Supervisors Duties: Supervisors reviewing Helix reports with employees during Pre-shift meetings.
- Continuous Improvement: Are supervisors, managers, and Engineers using the Helix Historian to track data and get feedback to floor employees?
Timeline Helix Deployment and Communication Plan
InSource Solution’s process of training and deploying your factory is key to having a successful MES adaption. Our success comes from our consultant’s ability to utilize the one-on-one time to train employees at their workstations when available individually. After the go-live stage, the InSource Systems Architect will stay at the plant to train all employees on the Dashboards, Reports, and Workflows. This process ensures that all supervisors, managers, and operators achieve adoption using the Helix. After the adaptation period, InSource ensures the team has a proper communication plan.
The Project Communications plan allows all levels of the organization to know what tasks need completion for a successful Helix engagement. The program allows for clear communication from the floor operators to the plant manager on outstanding tasks that require completion.
After the six-week training, the factories can implement the processes shown with the tools they learned. These factories were able to utilize the following:
- Dashboards, Reports, Quality Samples, and SPC Charts: Dashboards keep everyone informed on the plant’s status, and Reports give managers quick access to company data. Quality Samples and SPC charts keep the product in spec throughout the production run. The SPC charts allow employees to stay between the lines and produce quality products. Quality Exceptions alert plant personnel when a quality exception takes a product out of spec.
- Supervisors’ Helix Walk and Leaders Walk: The Helix Walk takes place twice a day and ensures employees comply with training standards and expectations. The one-on-one interaction with plant employees allows the operators to give real-time feedback to supervisors and managers. The plant and senior managers take a “Leaders’ Walk” that enables them back onto the floor. The operators enjoy the interactions with senior managers and have the opportunity to be transparent about plant issues they encounter.
- Weekly Report: The weekly report keeps each Helix engagement on track and moving in the right direction. The report covers completed goals and critical path identifications that could result in project delays.
- Adoption Matrix: The Adoption Matrix shows the managers the level of adoption of the Helix system by the supervisors. It’s a great training tool when counseling supervisors on the expectations and offers levels of expertise required to be successful using Helix.
- Helix Health Assessment: At the end of each Helix engagement, the assessment identifies areas in the plant that are performing well and areas that need improvement. Additional health assessments are scheduled 60 and 90 days after the initial evaluation.
- Change Impact and Issues Management: The Helix Champion gets a Change Impact Assessment. The Helix Champion and InSource Solutions meet weekly to ensure resolution for all issues if any.
After 60 days, we returned to the plant to assess the process and resolve any issues with the deployment. We love to return to assure what has been implemented works for the plant and its employees. We can ensure a successful deployment by returning to the plant 60 days later.
“What’s in it for me” with Systems Adoption
We like to implement a “What’s In It For Me” mindset during training. This mindset gets everyone focused on what Helix brings to the plant at each level for all employees. When we introduce this thinking, each employee sees Helix as a necessary tool for them to use. This mindset helps facilitate teamwork within the plant at all levels and creates a great work dynamic between employees.
As we finished the first three factory deployments, we found that teaching operators to run reports tracking their performance on production or waste is a game changer. With all levels of the organization using the Helix MES tool, production increases, quality improves, and communication becomes more effective.
At InSource, we take pride in our training methods and stand by our ability to change the dynamic of your plant. Utilizing AVEVA MES, we take any plant from paper and pencil to Dashboards, Reports, and a Quality Cockpit. Contact us today to learn how our AVEVA MES deployment can upgrade your plant.
Learn more about the AVEVA Helix Project here.