Creating the “HEY GOOGLE” Experience in Industrial Workplaces Blog
Cloud-based single source of truth across the asset lifecycle using AVEVA Teamwork
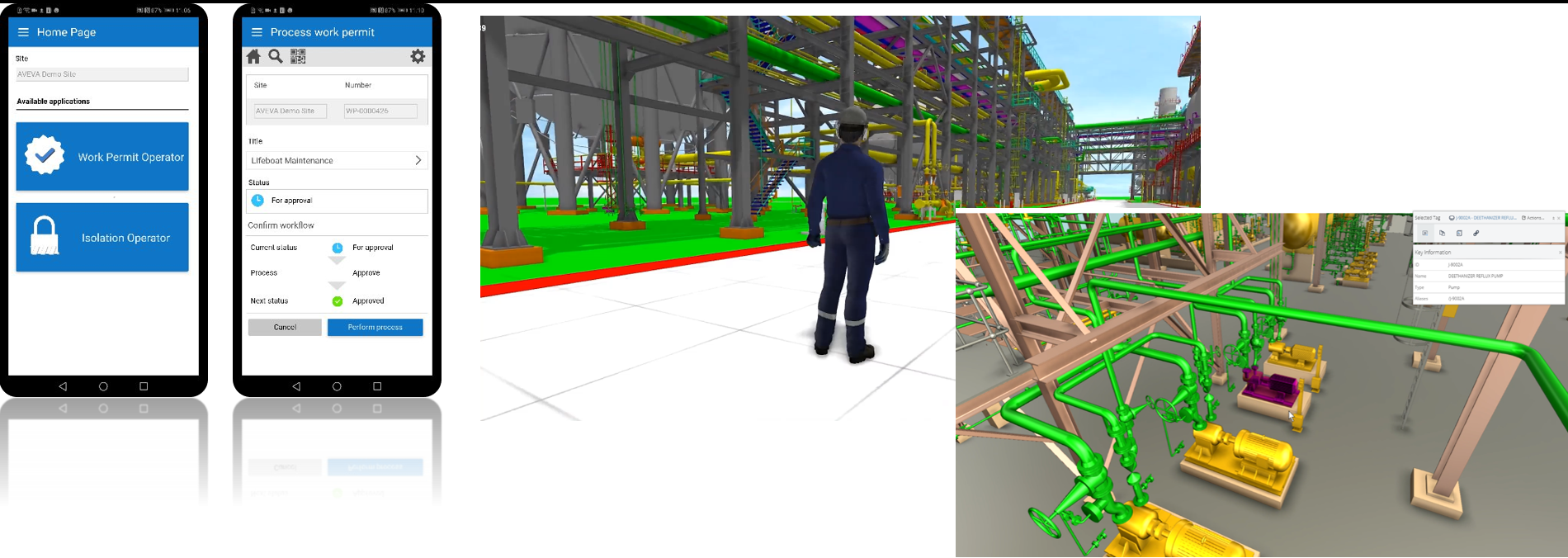
Accessing data in industrial environments can be challenging, unlike the seamless experience of finding information online. Manufacturers and industrial operators often deal with siloed data sources, leading to inconsistencies and difficulties correlating and visualizing information. This results in wasted time searching for data, impacting productivity. Products like AVEVA Asset Information Management Discovery (AIM) offer a solution by connecting workers with the content they need, creating a “Digital Twin” of assets. This cloud-based system provides universal access to data, 2D and 3D visualizations, powerful search capabilities, and secure data access. AIM improves transparency, efficiency, and decision-making based on trusted data, making it your new “Google for the Factory.”
Just think about how we access data today in our personal life. Gone are the big Atlas Maps and Encyclopedia Britannica. If I want to get information today, all I do is “Google” it. If I ask Google for information on a restaurant; I will receive the address, phone number, directions (in 2 or 3D), menu, pictures of the food, 360 degree inside and outside view as well as the website link. All the information I need to make an informed decision. All in a single view. As we move from our personal world to the industrial world it is a different experience. We face a few challenges having that same “Google” experience.
We all know that access to reliable information is critical to make informed decisions. So what prevents “The Google Experience?”
- The 1st challenge we face is the information is much more siloed in industrial environments. We, as manufacturers & industrial owner/operators have multiple disconnected sources of data. This often results in inconsistent and conflicting information. And then when you DO get the right data, it is very difficult to correlate or visualize all the information you need WHEN you need it.
- The 2nd challenge we face is specifically with engineering information. Around 4% of unbudgeted CAPEX is lost due to poor engineering information handover. Studies have confirmed that a savings of 15% of the total installed cost (TIC) of a project can be realized simply from effective engineering information management.
- Last but not least, the 3rd challenge we face is the amount of time wasted searching for information. In industrial work environments, we lose about 1 day a week of productivity searching for information. Just think about your own experience. How easy is it to find information on your control system, your corporate SharePoint, Box, your ERP system, website, or other applications? Now you may be able to find information from one of these applications but what if the information exists across multiple applications? How easy is it for you to correlate the information? Which information do you think of as trusted? Which sources are you concerned about being current or accurate?
Across all industries, maintenance and operations workers need timely and accurate information to support their daily activities. It is common, however, to see asset design models, maintenance information, manufacturers’ data, P&IDs, and other data stored in a variety of different formats in unconnected repositories. Most companies also have teams dispersed across multiple plants and various global locations all needing access to that information. This approach results in data silos and a severe lack of transparency, efficiency, and trust within organizations. In order to demonstrate regulatory compliance and guarantee safe operation, most leaders are looking for ways to remove the obstacles to delivering relevant and complete information to their workforce.
I have recently seen one solution worth considering. AVEVA Asset Information Management Discovery (AIM) is a product that connects workers with the content they need to do their jobs. It ingests data in various formats from multiple systems to deliver rapid, intuitive access to a “Digital Twin” with information that accurately describes the current condition of the physical asset, rather than how it was initially designed.
In short, this revolutionary product addresses all 3 of the challenges above. With AVEVA Asset Information Management Discovery, workers can access data across silos, including engineering & current operational information. It creates a cloud-based single source of truth across the asset lifecycle and thus saves significant time looking for information. Easy recall of documents and critical data translates into the ability to respond quickly to incidents, which in turn increases safety. The AIM system also improves organizational transparency and decision-making based on trusted data by going to the “best source” of the truth.
In summary, AVEVA Asset Information Management Discovery, is your new “Google for the Factory” It delivers:
- Universal access to your Digital Twin, allowing access to all informational content at any time.
- 2D and 3D visualization: intelligent, hot spotted P&IDs and 3D models that link back to the content referenced in the database.
- Powerful search capabilities
- Ability to organize and collaborate on asset data and documents irrespective of source or location.
- Secure data that is only accessible to approved parties.
- Continuous improvement with regular updates and feature enhancements constantly being pushed to the Cloud, without having to install any software updates or disrupt productivity.
- Reduced risk through native Cloud support for backup and disaster recovery
- Richer information about the operating plant and equipment to support document authoring, reviewing, and distribution process.
In your personal world you will still “GOOGLE” it to get information you need. Now with AVEVA you can “AIM” it to connect workers to accurate information they need to perform more effectively and efficiently. For more information, contact us today!
Want to learn more?
To learn more about the AVEVA AIM technology, register for this free event.
Contact us
To learn more about InSource Technology Adoption Services.