More than just technology – Industry 4.0 is also about the people
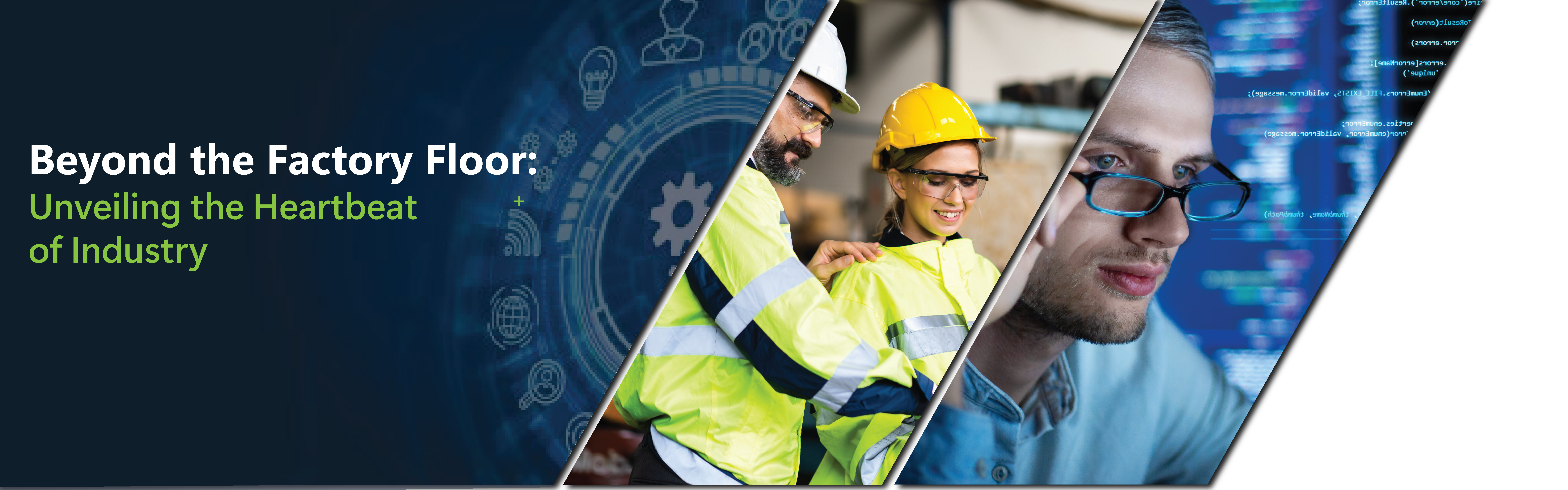
In the Manufacturing Industry, time is money. While factories are investing in new technology and software, we often see that the investment alone is not enough. The success of any technology or program installation frequently rests on the users and the partners chosen to implement the changes.
I have spent most of my career in the manufacturing sector, from designing and building to maintaining and optimizing. I have witnessed firsthand how technology and software have revolutionized the manufacturing industry on the macro level and transformed individual companies on the micro level. Nevertheless, one must be aware that simply investing in new technology and software alone is not enough to tackle all the difficulties in this space. The effectiveness of any new technology or software application frequently depends on the proficiency of a professional team in guiding, educating, and integrating personnel to utilize the technology so that the company can maximize the value of its investments. Industry 4.0 is about technology, but we must not forget that it is also about people.
Manufacturing businesses face various difficulties in the modern world, including heightened rivalry and shifting consumer demands. In the United States, we saw firsthand how something like COVID could cripple our supply chain and decimate production and profitability in many sectors. Many businesses have turned to InSource Solutions and companies like ours to boost productivity, cut costs, improve the supply chain, reduce waste, and raise quality in response to these difficulties. Even though these investments can be considerable, their actual worth depends on how well a company’s staff can use the hardware and software. Fortunately, as a full-service software solution provider, we can support clients through the ideation, implementation, coaching, adoption, and reinforcement stages after installation. That way, clients always have an advocate for their chosen solution.
The sustained success of any technology or program installation lies in the hands of the end users and local leadership. Given the fact that employees may resist new technologies or ways of operating, buy-in is crucial because change can be challenging. Although it is genuinely one of the only constants in life, change is still tough when an established order and protocol are being improved or revised. Because of this, training and adoption coaching is essential to assist employees in comprehending and accepting new technology. In our case, these “coaches” are made up of individuals who have a comprehensive understanding of manufacturing technology, operations, and the production process, as well as a keen capacity to interact with employees at all organizational levels in an effective manner. They can guide organizations past the initial growing pains because of their experience. They know that a well implemented solution makes work easier and less cumbersome for operators and supervisors, which can lead to an improved sense of morale and job satisfaction.
One of the primary advantages of having adoption coaches in place is that it may help to prevent and eliminate many of the common problems associated with change management. High-level techniques and processes are taught to leadership, so they have the tools to continue improving their workforce when the coach’s time is complete. This efficiently allows organizations to spread and mitigate risk by leveraging outside expertise. It also solidifies training methodologies for new hires and promotions within the client’s company. We have noticed that transparency and accountability among leadership and operators can make or break a coaching and adoption deployment. The decision to win and the decision to improve cannot be half-hearted. When data becomes available, the direction of improvement becomes clear, making success an informed decision rather than a wishful thought.
In this space, time truly is money. Downtime, just one aspect of operations that requires an automated solution for transparency, can be a lurking assassin of profit and efficiency. Due to the way downtime has been manually recorded for decades, it can be difficult to pinpoint how much time is lost and how often it occurs. Many operations still use pen, paper, and an Excel sheet to retroactively portray how equipment runs, leaving themselves open to large margins of error and questionable data. That is where your team of adoption coaches come in to work alongside your site team and integrators to build and train the equipment, operators, and leadership on how to automate that downtime capture process. This way, precious time and resources can be allocated from documentation of the “What” to resolution and improvement of the “How” and the “Why” of the issues causing the events.
In summary, manufacturing firms have an opportunity to protect their expenditures and ensure that they obtain the most value from their organizations by investing not only in new systems, software, and technology but also in developing and optimizing their workforce. Companies like InSource Solutions are uniquely equipped to meet these needs in a way that consistently creates winning outcomes for their clients. Prioritizing innovation in this manner has been proven to reduce, and in some cases eliminate, many of the common problems associated with the steps to improve, up fit, and recreate manufacturing processes for the advancement of Industry 4.0.