No More Clipboards or Paper Checklists
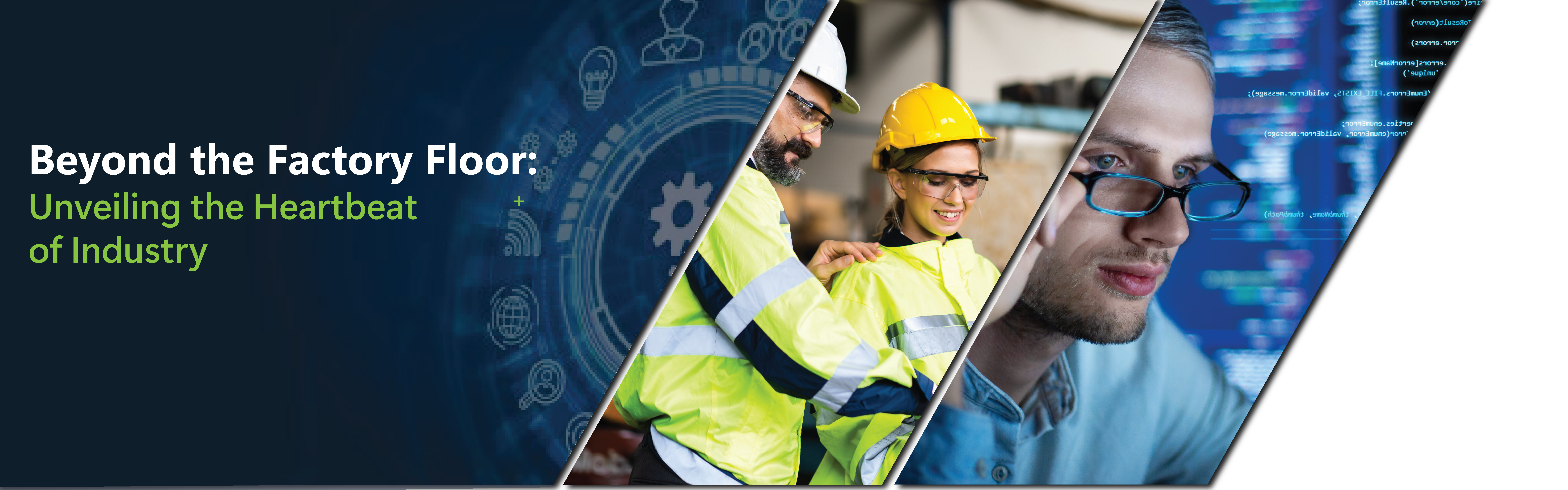
With digital transformation becoming a hot topic, have you ever wondered how many tons of paper are used in “clipboard rounds” in manufacturing plants annually, and then deposited into file cabinets never again to see the light of day? No – just me? OK then, follow along just to humor me. So that we have a number to argue over, consider the following.
The U.S. Bureau of Labor Statistics says that, as of Q3 2020, there were 360,078 manufacturing establishments (let’s call them “plants”) associated with the NAICS codes 31-33 (Manufacturing). If we assume that each plant uses 2 reams of paper per month in support of manually collected round information, then the answer to my original question would be 21,605 tons – just in the U.S. I’d be willing to bet the number is MUCH higher than this, but that’s good enough to support this thought experiment.
If you’re responsible for plant operations, the amount of paper consumed isn’t the real problem. I’m certain that you could identify a great many downsides to collecting plant data the same way it was done in 1951. Some things that come to mind for me:
- The possibility that the “round” is completed in the most comfortable part of the facility, not necessarily where actual conditions can be observed, documented, and acted on.
- The possibility of transcription errors when the data is loaded into a spreadsheet or other system (if that even happens).
- The lack of a mechanism to highlight out-of-tolerance values and prescribe actions for the user in the moment.
- Difficulty merging the manually collected data with other data sets.
- The inability to provide trend information to the user in the field, to aid in the visual identification of impending problems.
- The possibility that no one other than the person collecting the data ever sees it.
Much has been written in the last decade about the need to digitize data on the shop floor, yet a surprising number of plants still operate with clipboards. Why is that? It turns out that manufacturing people, like all people, tend to resist change. Even when it is obvious that better ways exist, the amount of inertia involved in making even a simple change can be insurmountable. This has sometimes been compounded by the complexity of digital transformation.
Consider whether now might be the right time to finally move your plant into the digital transformation age. Modern software has significantly lowered the barriers to entry, both from a cost and effort perspective. Powerful, low-cost devices abound. If you’re not reading this blog on one, then there’s a very good chance that you have one within arm’s reach. Built-in cameras process barcodes and QR codes to verify your location and bring the right information to you in an instant. Standardized peripherals, like thermometers, RFID readers, and vibration sensors, greatly enhance the types and quality of data you can collect.
How much effort does your organization invest in “clipboard rounds” today? What real value do you get in return? Could digital transformation tools allow you to seal off some of the value leaks in your operation?
You might save a few trees. More importantly, you might unlock real value from an activity that you’re already doing!
If you are looking for more information on digital transformation or AVEVA Mobil Operator, contact us today!
AVEVA Mobile Operator Rounds
Join us for a look at a tool that can easily digitize your Operator or Maintenance rounds.
You might save a few trees.
More importantly, you might unlock real value from an activity that you’re already doing! Agree? Disagree? Drop me a note and let’s discuss.