Paper to Glass. Always a Worthy Endeavor…Now it’s essential
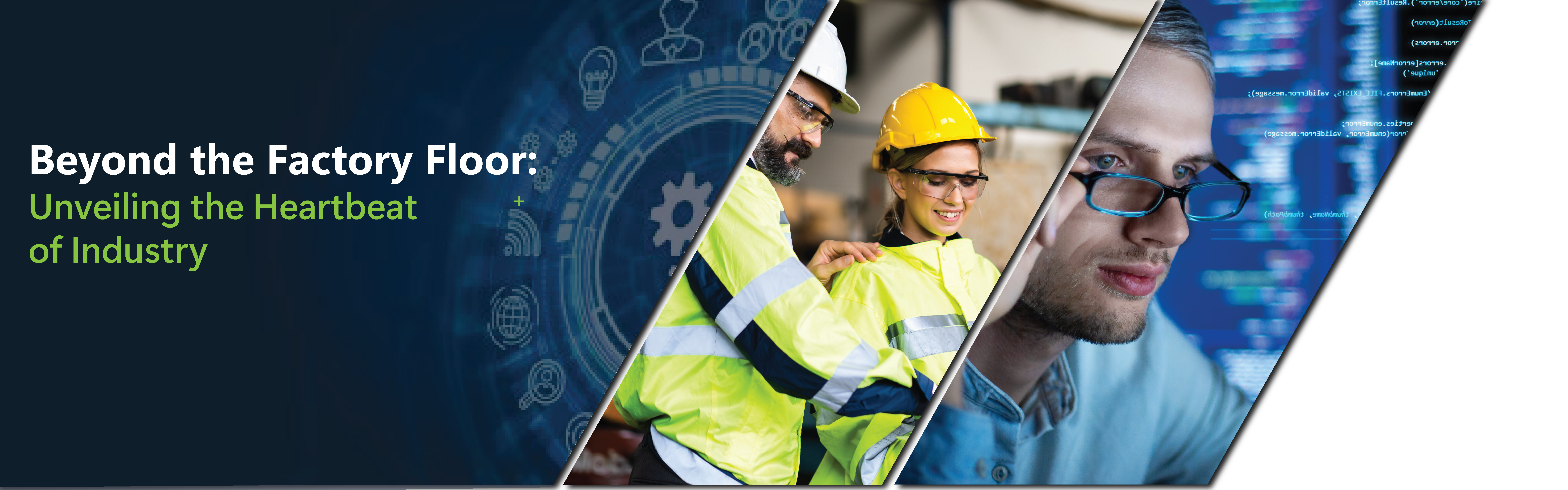
Ever since the dawn of the Industrial Age (circa 1790 U.S), manufacturers have been looking for a better way run their business and to track their progress and productivity. There have been many improvements in the sources of power used (manpower to machine, wood to coal, coal to oil, oil to gas, gas to solar and back again to wind!), and automation of the mechanical processes; in particular, the assembly line. That lightly covers the power and inventions. However, many paper-based processes and procedures have stayed stubbornly frozen in time and when it comes to tracking/recording production data or communicating between production teams or standardizing procedures, many manufacturers are still using a centuries old method of recording; paper and a clipboard!
Paper still has its place and will likely never be totally replaced by digitization but in manufacturing there is an ever-stronger argument to move toward digitized information commonly called “paper to glass.” And then comes COVID-19. Now we’re hustling to eliminate paper as a surface born area for contamination. There will eventually be a COVID-19 vaccine and that specific fear may subside, but manufacturers are now acutely aware of an essential tool for increasing efficiency and safety in the workplace…Paper to Glass.
As with any transition “you won’t change until the pain of not changing exceeds the pain of change” I know this sounds a bit harsh, but many manufacturers do not want to fix that which they perceive as not being broken. Now we see new and compelling reasons to change. As with any change process the initial movements are toughest on your routines, but the positives outweigh the relative inconveniences seen in these early stages.
The following very basic steps are required to make your paper to glass conversion as seamless as possible:
- Defining – what will the vision look like upon deployment? During this stage it is best practice for leadership to let their vision be known to those most affected by the upcoming change. People need a bit of pre-warning that a new technology is coming to the shop floor. It is also best practice to get those most affected by the digitization to work on the team in charge of creating how these changes will play out in the various departments. If possible, having a subset of the facility chosen as the pilot site will make the transition much more palatable with the workforce as opposed to changing the entire facility all at once. This gives time for modifications and lessons learned in a smaller scale with less interruptions to the work processes. Of course, if your reason for changing is safety, as with the COVID-19 example, then a big bang approach may be required.
- Choosing – which technology tool fits your needs best? By the time you get to this stage you have a good idea as to what you want the technology tool to do. Any good paper to glass tool, at a minimum, needs to do just that, convert the current documents to a digitized form. Aside from the basic conversion, what else should a paper to glass technology enable your plant to do or do better? Do you expect the input or gathered data to have conditionality (data warns you when information is out of range)? Do you need report writing capability? Will you want connectivity to other systems in your plant? How flexible does the system need to be for expansion to other site/divisions? How easy is it to get your new system up and running? (hardware requirements, etc.)
- Gathering – knowledge (and paper!) Now that the people are prepared to fulfill the vision of going paperless (or at least near paperless), it is time to better understand the pilot area chosen as to how it operates. Where does the data originate and where does the data go? How is the data being used? By whom? How often are employees interacting with the data? Is there any manual data being gathered that could be queried from PLC’s or historians? Are supervisors and operators using duplicate forms for gathering the same information? Is the current data reliable and believable? Why or why not? (Tip: If the data is not believable, you better fix that data gathering process first)
- Deploying – the system and the training Up to this point you’ve been working on the preparation steps to ensure your paper to glass transition goes well; now it is time to get the system deployed and the training of end users started. Since you have included those most affected in the front end of this process the training segment should go well. Since you are focusing on a pilot to roll out the new technology to the initial group of trainees, the scope should be rather small and manageable. Training should take only a few sessions to get folks comfortable with logging in and performing basic functions. The first few days of going live with any system is typically the most stressful and it is common practice to have operators use their old paper process along-side the new digital method. This is an opportune time to reinforce expectations as to how the system should be used, part of the benefits of going digital is there should be an increase in standardization of work.
- Auditing – follow-up on the system use (with continual improvement) Now that the system has gone live and is in use it is time for auditing of the process; are people using the system as expected? This is a critical time in any systems’ lifecycle as the management team can reinforce good behaviors and correct those behaviors that do not support the overall vision. Auditing needs to be done for all the users to be fair and auditing does not just see how the operators are complying, but is the system/technology doing what it is supposed to do? The results of these early audits are vital to ensuring bad habits do not become permanent ones and the system is being used to its full potential.
As we have seen in this short blog, the move from paper to glass does require some planning, but the outcome is certainly worth it. Leadership drives the change but assigns the end users a big part of the change and how it will be utilized. This type of leadership greatly improves ownership and compliance to the system.
A paper to glass implementation should improve standardization, paperwork and duplication of effort should be drastically reduced, and you’ve moved into the 21st century with data management! Your ability to search and analyze the captured data has sky-rocketed! And of course, with appropriate hardware investment, you’re not passing a potential contagion from person to person. A worthy endeavor indeed.
InSource has over 30 years’ experience in Digital Transformations. Call us, we can help.