The Connected Worker Culture Shift
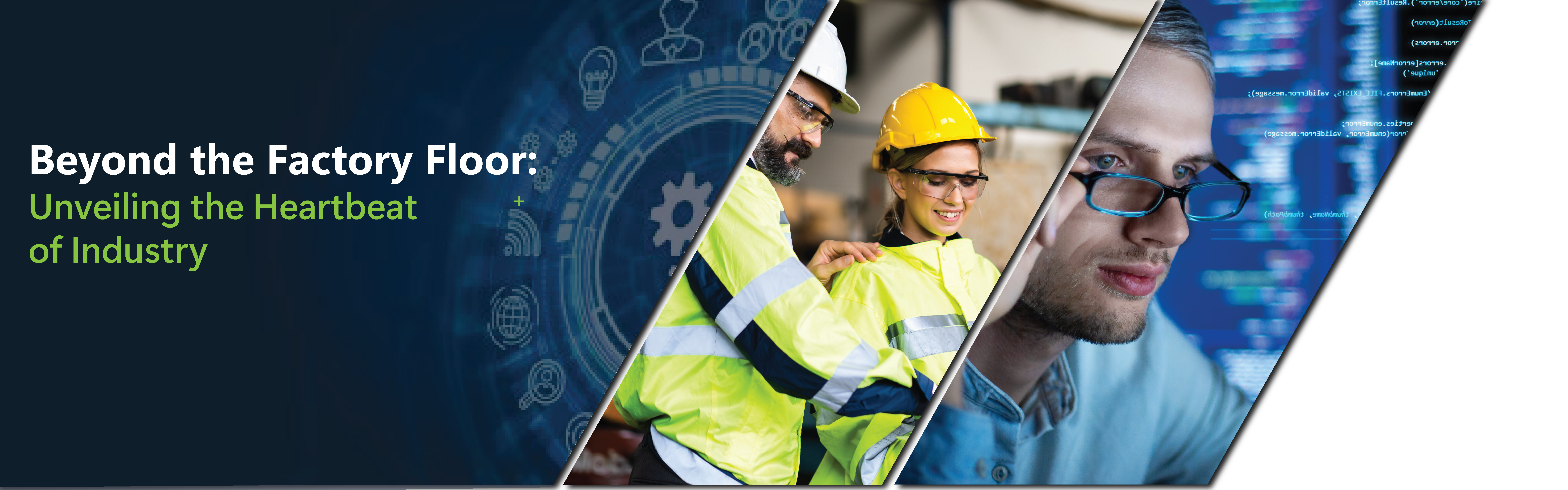
Steve Jobs’ introduction of the Apple iPhone in 2007 was nothing short of revolutionary. But contrary to what our perception of that announcement may be now, there was quite a bit of consumer skepticism in the beginning. After the announcement, concerns mounted as the design was so drastically different than the typical phone at that time. Seemingly trivial now, common concerns across the consumer base ranged from the battery not being accessible to the lack of a keyboard and the limited number of phone carriers. All of this, in addition to the fact that it was far more expensive than all the other phones on the market, made it seem like a poor investment. The skepticism even came from other individuals we’d label as trailblazers – Microsoft CEO Steve Ballmer was quoted stating that with the high cost and lack of key features, “there’s no chance that the iPhone is going to get any significant market share.”
Initially, skepticism caused a slow uptake in sales and necessitated price reductions in the first year. This was primarily due to consumers’ hesitation to deviate from their established preferences and comfort zones. However, as time passed, early adopters played a crucial role in demonstrating the iPhone’s enhanced efficiency, gradually paving the way for the wider population to recognize its benefits. The touchscreen innovation brought efficiency to navigate through content, and the elegant internet browsing capability far surpassed what the Blackberry was able to provide. Users slowly began to realize that this new way of operating seamlessly integrated camera, web browsing, and phone capability into one device. This device, which had once been seen as an innovation that would go nowhere has now revolutionized the way modern society communicates, learns, and ultimately lives.
Now, apply that thinking to connected worker technologies in a manufacturing environment. “Connected worker” is the new buzzword when we talk Industry 4.0 – but manufacturing has been an industry that traditionally has never been on the cutting edge when it comes to innovation and new technologies. Specifically regarding the manufacturing workers, although digital technology has been available for decades, they have continued to rely on printed manuals, paper forms, and radio communication as primary tools on the job. Connected worker tools aim to optimize this way of working through digitization; however, similarly to the introduction of the iPhone, face skepticism and adoption challenges as these technologies completely change how these workers operate.
Workers who have relied on paper checklists for decades may have doubts about the technology’s capability to effectively save and store the information for future reference. Similarly, individuals who have grown accustomed to physical manuals or binders of work instructions at their workstations may find it easier to locate the information they need in those formats rather than on a tablet. While digitizing information has undoubtedly made it quicker to access what we require in our personal lives, we often encounter hesitancy when contemplating implementing such changes in a manufacturing setting. This reluctance may stem from a resistance to deviating from familiar work methods or a belief that existing processes are already optimized. But just as Apple did, once we overcome the initial hesitation and skepticism, connected worker technologies have the potential to do much more than simply digitize our processes – they fundamentally transform an organization’s culture.
Here are a couple of ways that technology is laying that foundation for a manufacturing cultural paradigm shift:
#1: Workers are now taking more ownership.
By giving our frontline visibility to real-time information about their performance and key areas of improvement, we not only raise awareness but also spark healthy competition. Below is an example of a production floor dashboard designed specifically for this purpose. Providing our employees with data on metrics such as shift performance, primary reasons for downtime, and performance trends empowers them to make quick and effective decisions. Displaying performance by shift fosters friendly rivalry among different teams, which can be further encouraged through periodic incentives from leadership. Showcasing the primary causes of downtime promotes a holistic awareness on the plant floor, igniting problem-solving initiatives, enhancing communication, and facilitating best practice sharing between employees. Knowledge plays a pivotal role in driving progress and success in this context.
#2: The workforce is more agile and adapts to change easily
With greater awareness and access to information comes the ability to adapt to change and do it much faster and more efficiently than ever before. Connected worker platforms, like AVEVA Teamwork, enable users to act on the information given. The visual representation below exemplifies an issue posted in the Teamwork application. This platform enables frontline workers to identify and describe the issue they are experiencing while also providing the option to attach supporting materials such as pictures, videos, external documentation, or relevant links. By sharing these resources, users can enhance the visibility of the issue and facilitate interaction and collaboration among other team members. Those deemed ‘experts’ will be notified immediately after posting – generating instantaneous awareness and minimizing the issue’s impact. From there, users can comment to assist with resolution and ultimately create troubleshooting instruction that can be stored in the application for others who may experience a similar issue down the road.
#3: Workers work more efficiently, allowing more time for value-added activities.
Another application that can generate tremendous value is AVEVA Work Tasks. Work Tasks is an application that allows organizations to digitally build the forms that employees have historically completed on paper. You can then model and automate the business processes these forms are designed to follow. Automatic notifications or escalations can be created based on how the user answers individual questions on the form. Or the ability exists to create integrations between disparate systems like CMMS, MES, or LMS, to name a few. Because users can use the Work Tasks mobile application on a tablet at their workstation, manufacturing operations no longer need to stop for administrative purposes. Furthermore, workers now have more time for value-added activities that are proven to improve performance, like autonomous maintenance activities and problem-solving initiatives. The image below displays an example of a digital form accessed on a mobile device and a process flow built to manage exceptions, notifications, and approvals required to run production.
#4: Promoting Employee Retention Amid the Labor Shortage
In addition to the changing desires of those currently working in manufacturing, the industry also faces a challenge in attracting new talent to work within the factory environment. Technology and automation are completely changing the nature of manufacturing; however, the perception of factory work among potential recruits continues to be outdated or overshadowed by a misconception. Furthermore, manufacturers are encountering difficulties in showcasing the opportunities for growth, innovation, and career development that exist within their facilities. With these gaps in mind, it becomes crucial for manufacturers to emphasize the adoption of modern technologies, the integration of digital tools, and the cultivation of a dynamic and engaging work environment to appeal to the aspirations and expectations of the younger workforce.
Adopting modern technology in manufacturing not only helps attract new workers but also plays a crucial role in retaining existing talent. By implementing advanced technologies and digital solutions, manufacturers can create a more engaging and fulfilling work environment that aligns with the preferences of the current workforce. Automation, robotics, and smart systems can reduce the physical demands of repetitive tasks (which are often less desirable within the workforce), allowing workers to focus on higher value-added activities that require problem-solving skills and creativity. By embracing modern ways of working, manufacturers can not only address the skills gap but also foster a culture of innovation, job satisfaction, and retention, ensuring that their workforce remains motivated and committed to the industry’s continued success.
When employees are presented with the information they need and have an efficient and effective means of acting on issues as they arise – this paves the way for rapid continuous improvement. Awareness and agility are catalysts to change and as we know, the technology brought to market is forever expanding and maturing. Empowering employees allows new and cutting-edge technology to be brought in and implemented much faster. Solutions like artificial intelligence, machine learning, or AR/VR now have an actual seat at the table. Just as Apple played a key role in innovating society’s communication, manufacturing connected worker technologies have the potential to shift company cultures to that of quick learning and fast adapting organizations.