Removing Roadblocks From your Digital Transformation Using X0 Solutions
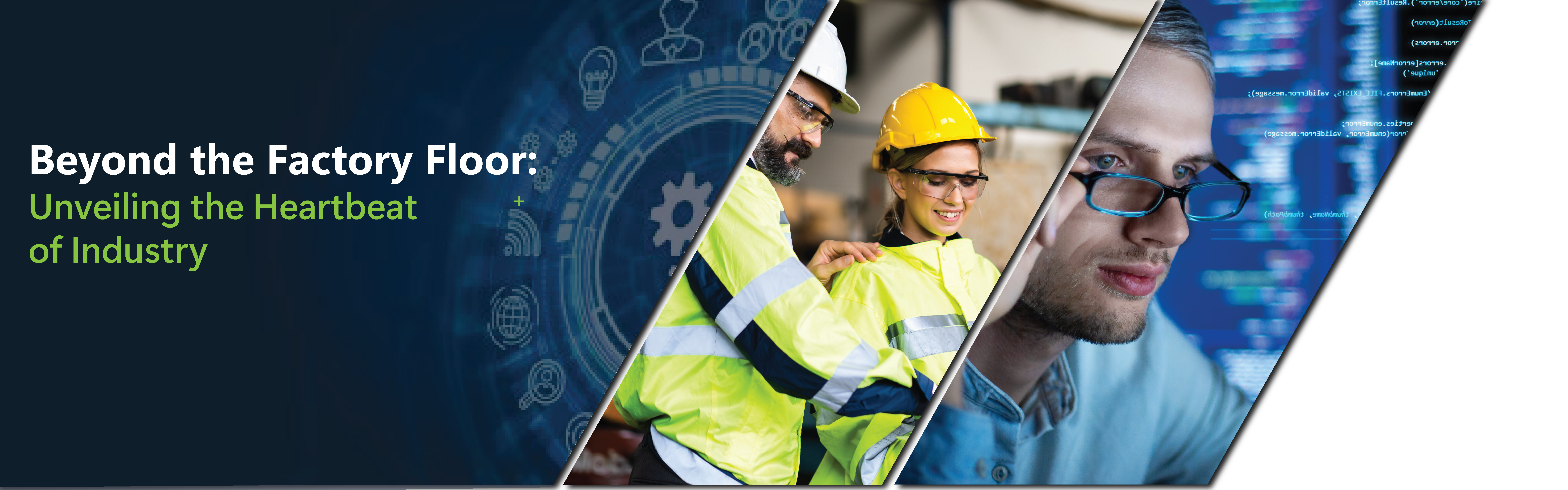
Your factory’s Digital Transformation can be free of roadblocks when you know what to expect. While on your journey to digitize, having the right solutions can ease the transition for your entire workforce and help remove any hurdles.
For as long as manufacturing has existed, increasing efficiency has been a primary focus for factories. The question is always, “How can we make more for less?” In the digital age, data analytics is the answer. The more we collect relevant data, the more it allows us to fix issues causing machine rejects and downtime, thus increasing our output without adding human resources or additional equipment. However, there are a minimum set of requirements to data collection that some manufacturers see as roadblocks to starting their digital transformation journey.
Roadblock 1: Network Connectivity
Unfortunately, it is common to find facilities where the manufacturing equipment is not connected to an internal network. We see this, especially with older facilities that were built before the concept of data collection existed or at newer facilities where plant network infrastructure was an afterthought. Either way, the hurdle to collecting data can be off-putting to plant leadership who think the only solution is a costly network infrastructure upgrade project.
Roadblock 2: IT Resources (Software deployment and maintenance)
Even if the facility’s manufacturing equipment is connected to a network, many companies do not have the necessary IT resources to support large-scale server builds and software installation and deployment projects. Furthermore, the cost associated with licensing fees, simple licenses for data collection software, Microsoft Operating Systems, and Microsoft SQL can create concerns around cost and deployment. IT teams can also be concerned about the backup strategy that they will need to employ to ensure data integrity.
Roadblock 3: Software Configuration
Once a software solution is installed on the IT infrastructure, there is still work to be done to configure the solution. Defining OEE calculations and collecting relevant machine data points that facilitate those calculations can seem daunting to facilities that have never undertaken the task. There is also the task of validating the collected data to ensure it is an accurate representation of the manufacturing process. Finally, the configuration can also pertain to user access right and continued administration of the solution.
Removing the Roadblocks: InSource X0 Downtime
X0 Downtime is InSource Solutions out-of-the-box equipment downtime tracking and OEE solution built on AVEVA’s cloud-based Insight platform. AVEVA Insight provides a secure and managed solution for collecting, storing, and visualizing process and performance data that can be accessed from anywhere with internet access. It can also be accessed via your mobile device using the Insight iOS or Android application. However, the real benefit of the X0 Downtime solution is InSource’s configuration and deployment services, which can be tailored to meet the specific needs of your factory. InSource will work with your team to remove the common roadblocks described above to deploy a fully functional machine downtime tracking solution.
Do you have limited network connectivity? InSource can deploy remote IoT devices to collect data without having to deploy expensive network infrastructure. Is the expense, deployment and support of a server-based software platform delaying your project? Allow InSource to deploy the solution for you on our preconfigured hardware. There is no need for your IT team to acquire expensive server licenses and deploy additional hardware. Insource will provide the hardware with all the necessary licenses for the solution.
Does your team lack the time or expertise to define the necessary data to collect to accurately track your equipment? Let InSource work with your team to define the data structure and configure the downtime calculations for you. We will ship you a prebuilt solution ready for deployment. All you have to do is plug it in and connect it to your network. InSource will do the rest.
Downtime tracking Is one of the fastest ways to increase plant efficiency. Once you can identify and categorize your downtime causes, you can quickly address them to increase your plant performance. Even though this is widely understood in the industry, some facilities are hesitant to enact downtime solutions due to perceived roadblocks they are facing. Push past those roadblocks and put InSource’s team to work for you. X0 Downtime will be sized for your environment and preconfigured, on InSource-supplied hardware, by our engineering team before deployment at your site. This removes the need to have an internal team dedicated to delivering a solution at your facility. It also removes the need for internal IT resources to provision new servers or acquire new licenses.
Learn more about InSource X0 Solutions…
and how our approach can revolutionize the way your data is collected, stored, utilized and maintained.