We Miss You Reliability. Please Call Home.
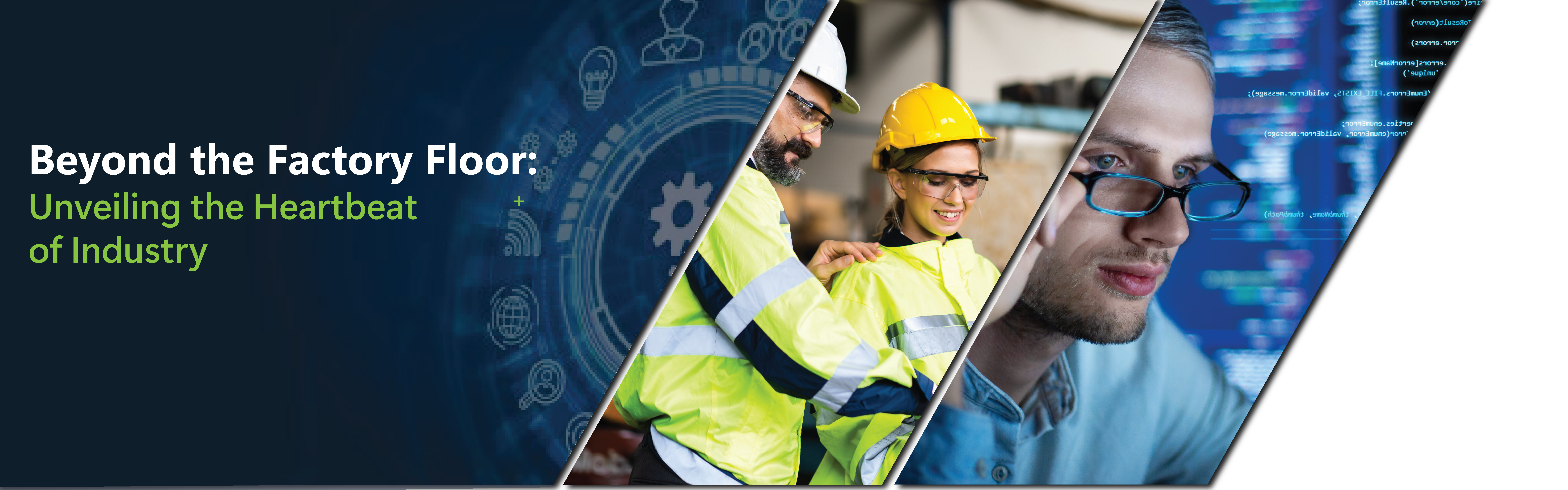
Your organization has invested heavily in asset performance technology to support and enable a reliability culture, but something seems to be missing. The new CMMS (Computerized Maintenance Management System) is functional with an updated asset hierarchy and integration to the parts warehouse and purchasing. It’s working better than expected. The massive activity of analyzing and evaluating PMs (Preventative Maintenance Activities) has been completed. There is a mix of run to failure, time based, usage based and condition-based PMs. Intervals have been systematically extended beyond OEM recommendations. Pre-staged preventive maintenance kits have been analyzed and adjusted for actual parts consumed. The new predictive maintenance tools are working well. The historical records, with adjustments for outliers, have created a solid starting point for the ongoing machine learning. Several potential catastrophic failures have already been averted…So, what’s missing?
A culture of reliability. The best of breed tools are in place at considerable cost to the company and there is a growing dependency on their use. However, there has not been a change in the culture. Technicians are still basically reactive. Instead of waiting for equipment to fail, there is a tendency to wait until the technology initiates a work request. The maintenance department, now called “reliability”, still embraces the fireman mentality. They perform routine work until an outside force requires attention. The maintenance department always considered themselves critical to and independent from the rest of the organization. They haven’t always seen the need to collaborate with other departments. Now with the latest and greatest technology tools the lack of collaboration is even worse. Underneath, there is still a reactive culture in this organization instead of a reliability one.
This points directly to an InSource dictum: “Technology Alone is Not Enough”. It takes the proper integration of People, Process, and Technology to deploy and sustain a successful solution. One of the tools that InSource uses when evaluating an organization is the Maturity Matrix. The Maturity Matrix is a framework to focus on the current state of an organization. It highlights current organizational status, areas that need focus / development, and provides a foundation for success. The categories evaluated are People, Process, Technology, and Disciplined Execution. This tool can be applied at the department / function level or for the organization. A Maturity Matrix evaluation can be conducted as part of the development of a new technology solution or it can be conducted as part of getting an unsatisfactory solution back on track.
The People category of the InSource Maturity Matrix evaluates the team’s level of ownership. Do the techs come to work just for the paycheck or are they stewards of the company resources and have an ownership mentality? They may be well-trained, but do they act in the company’s or their own (or department) interests? What is their relationship with the rest of the organization, particularly operations? The challenge here is to expand their mindset and integrate them into the greater team. Organizations with high reliability have support areas that tend to be responsive and interactive with operational needs. Department silos are part of the past. A reliability culture is one of employee ownership and initiative.
The Process category looks at the incorporation of systematized and well-defined processes in completing the work. Are there standard procedures that are known and complied with or is every event handled ad hoc? Is there a foundation for process optimization? Are standards actively followed-up on and reinforced or are they in binders gathering dust? When processes or equipment change are standards updated to reflect these changes? Beyond initial training, are periodic audits conducted to validate that employees are actually working to the process standards? What remedial / reinforcement training occurs with employees? To drive improvement and increase overall organizational reliability there needs to be an agreed starting point. Solid work processes that are trained and reinforced are foundational for a reliability culture.
In the previous example, the Technology category would rate fairly high. They are way beyond the basics of paper and spreadsheets to manage equipment and process reliability. However, Technology is only one component of a reliability culture and technology alone does not ensure one.
Disciplined Execution is bringing all the pieces together in a consistent, methodical way. Technology without proper integration with the People and Process results in execution that is inconsistent at best and probably very reactive at most times. A high rating here means that the organization is structured, methodical and adaptive. This is critical for an organization to embrace and adopt if they seek a culture of reliability.
Establishing a reliability culture goes beyond just providing the maintenance department with the newest tools and technology. A reliability culture is one of employee ownership and initiative with solid work processes that are trained and reinforced, along with the enabling technology. Tools, such as a Maturity Matrix evaluation can provide a means to objectively understand where an organization is and identify any alignment issues. It can be used in developing a road map to an organizational culture of reliability.
InSource has the experience and expertise to objectively assess your organization and develop a road map for a true reliability culture. Click to learn more about our asset management and reliability solutions.