Trends in Manufacturing for 2025: Insights from Industry Leaders
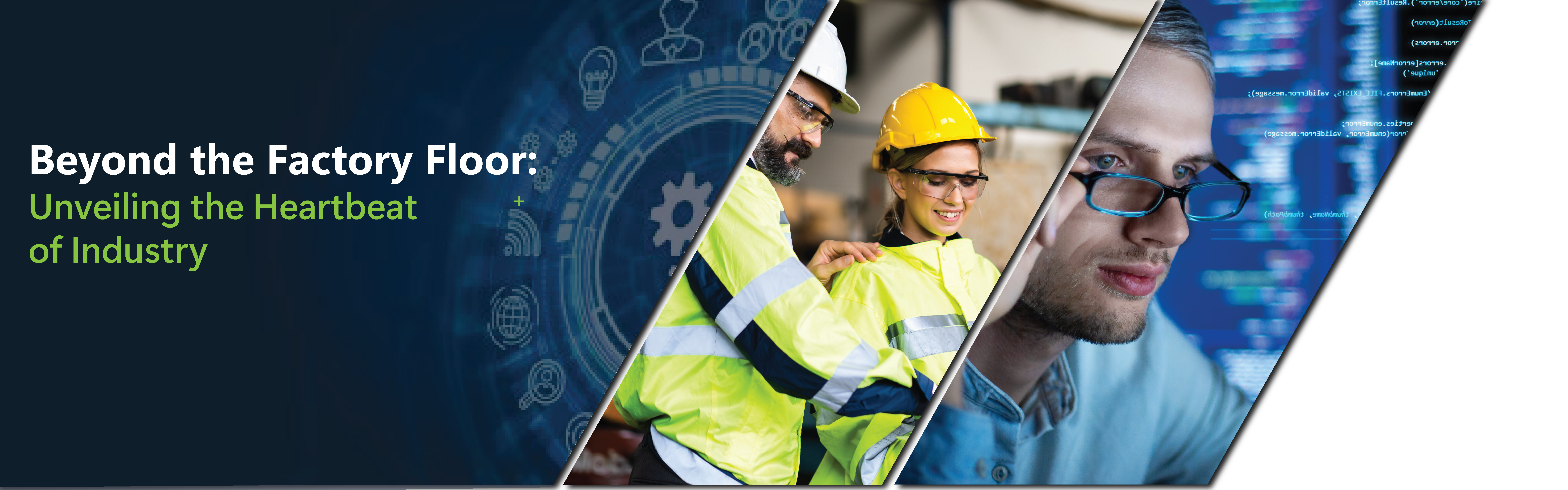
In a recent conversation, Kevin and Rob shared their perspectives on the key trends and emerging technologies set to shape manufacturing and industrial operations in 2025. Their discussion focused on the challenges and opportunities these innovations bring, providing valuable insights for industry professionals navigating the future. The conversation also included real-life examples, showcasing how these trends are already being implemented in industrial environments.
The trends shaping manufacturing in 2025 such as cloud analytics, digital twins, servitization, and workforce evolution, offer the potential to transform the industry. By focusing on specific outcomes and adopting a lifecycle approach to innovation, manufacturers can ensure these technologies deliver lasting value. Success depends on effectively balancing technological advancements with practical, people-centered strategies to drive the industry forward.
Cloud and Advanced Analytics
Cloud-enabled analytics are driving significant changes in manufacturing by offering scalable solutions and improved interfaces that make data tools more accessible. These platforms are becoming increasingly user-friendly, enabling a wider range of users, including those without technical expertise, to engage in data-driven decision-making. However, the success of these tools depends on clearly defining the specific outcomes manufacturers aim to achieve, rather than relying on generic data analysis. The integration of AI enhances these tools, allowing manufacturers to extract actionable insights from large datasets. Focusing on specific outcomes rather than general problems ensures that these technologies deliver meaningful results.
Digital Twins
Digital twins, virtual representations of physical systems or processes, are another game-changer. They can be data-oriented, simulating conditions for analysis, or physical, providing 3D visualizations of equipment and processes. These technologies are useful in training environments, where they help accelerate the skill-building process for less experienced workers. Creating effective digital twins requires addressing challenges in data contextualization, ensuring that the digital model can compare different conditions, such as similar lines in different plants or products. Digital twins also play an important role in advanced analytics, offering a foundation for predictive and prescriptive insights.
Servitization and Outcome-Based Models
The shift from selling products to providing outcomes as a service is gaining traction. This model, known as servitization, allows manufacturers to subscribe to services like “uptime as a service” or “yield optimization.” These services combine technology with expertise to ensure desired outcomes, addressing both operational challenges and workforce gaps. Unlike traditional approaches, servitization leverages real-time monitoring and action to prevent equipment breakdowns and optimize performance, going beyond just delivering reports. This approach is already visible in areas like predictive maintenance, where real-time monitoring replaces traditional methods.
Workforce Evolution
As manufacturing undergoes transformation, the workforce must adapt. New tools and technologies, such as large language models, are making it easier for workers to access and apply complex knowledge. These models also help bridge communication gaps by allowing operators to query procedures in multiple languages, making critical knowledge accessible regardless of linguistic barriers. Multilingual AI tools can bridge communication gaps, enabling operators to query procedures in their preferred language. Additionally, AI-powered workflows guide users step by step, helping them complete tasks more efficiently and reducing reliance on prior experience. These innovations help address the skills gap by equipping workers with the resources needed to perform tasks efficiently, even with minimal prior experience.
Digitization, Digitalization, and Transformation
The terms digitization and digitalization are often used interchangeably but have distinct meanings. Digitization involves converting analog processes into digital formats, while digitalization focuses on using digital tools to optimize and enhance operations. Both are stepping stones toward digital transformation, which represents a shift to integrating technology into every aspect of manufacturing. Focusing on digitalization enables manufacturers to enhance processes and bridge skill gaps by providing intuitive tools that empower workers to adapt to evolving industry needs.
The Role of Innovation Innovation is no longer optional in manufacturing; it is essential for staying competitive. Embracing a digital-first approach is key to attracting and retaining talent while driving operational efficiency. The focus must go beyond implementing technology to ensuring it empowers workers and enhances processes. By aligning technology with human needs, manufacturers can create sustainable, long-term improvements.
Stay ahead of the curve! For the latest insights, trends, and expert perspectives shaping the manufacturing industry, check out our Blogs page today. Dive in and discover solutions to drive innovation and success.
Watch on YouTube
View the full episode of The Edge of Innovation Podcast.
Latest Updates
-
Blog
Operational Technology Support, Reimagined with InCommand
-
Resource
InSource Solutions donates Festo Mechatronics Learning System to Piedmont Technical College to support advanced manufacturing education in South Carolina
-
Event
Dream Report Fundamentals – Live Online
19 Aug - 21 Aug, 2025 -
Event
InSource Innovate 2025
23 Sep - 26 Sep, 2025