Pima County
Pima County reduces operating costs, increases efficiency and improves safety at wastewater reclamation facilities with implementation of Situational Awareness strategy using AVEVA automation solutions.
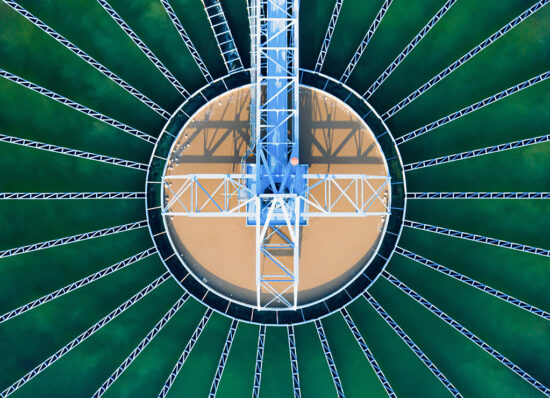
Goals
To ensure capture of institutional knowledge of current workforce for effective training of future operators.
To employ an effective Situational Awareness strategy enabling personnel to effectively understand and address operations of the facility.
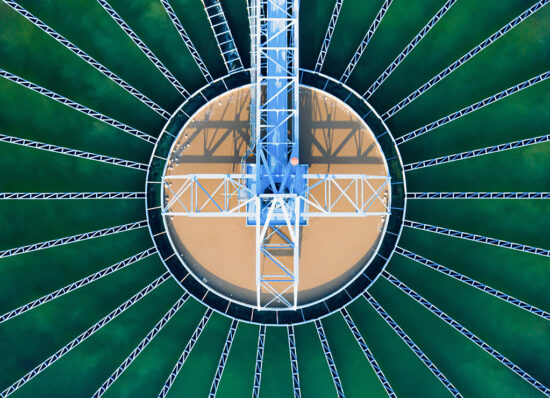
Challenges
Management of more than 60 million gallons of sewage each day to support the region’s population of more than 1 million people.
To take immediate action when alarms sound alerting operators to issues within the plant.
With assets spread out over more than 700 miles, operational management is difficult.
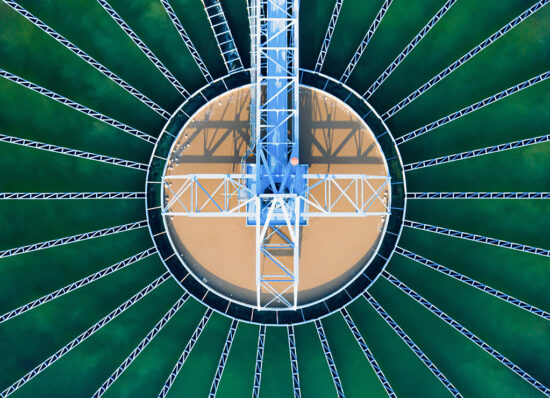
Results
Capacity of the plant has doubled resulting in a 50% increase in operational efficiency.
Overall energy consumption has been reduced by 10%
Current staff levels were maintained, while still achieving significant operational improvements.
“Institutional Knowledge” is captured to train future workforce, successfully addressing concerns of the facility’s aging workforce.
Sophisticated Data Mining capabilities resulted in the county receiving a $362,000 rebate check from the local utility.
With a population of one million people, the department manages an average daily flow of about 60 million gallons of water.
Using an AVEVA HMI and SCADA solution based on Situational Awareness and a mobile workforce system, the Pima County Regional Wastewater Reclamation Department provides management and maintenance of the county’s sanitary sewer system.
Serving a population of around one million people, the department manages an average daily flow of about 60 million gallons of water.
“We manage 3,700 miles of sewer lines stretching across a 700 mile area,” said John Sherlock, deputy director for treatment at Pima County. “Add in two metropolitan treatment plants, seven sub-regional facilities, 27 lift stations and 77,000 manholes, that’s quite a bit of ground to cover.”
The county’s Tres Rios Water Reclamation Facility has been recently upgraded from a “high purity oxygen conventional pollutant removal” technology to a five-stage “bardenpho process” that performs complete biological nutrient removal (BNR) of phosphorus and nitrogen.
“Our typical ammonia value coming into the plant is between 30 – 40 parts per million,” Sherlock said. “With our current treatment technology, we remove about 99% of that, resulting in the plant’s typical discharge of about one part per million ammonia.”
As a result, Pima County facilities have the highest nutrient removal levels required by both federal and state regulations to protect water quality.
Automation Plays Critical Role in Water Quality
Automation plays a critical role in the successful operation of the state-of-the-art Tres Rios Water Reclamation Facility. The automation system used to operate the facility is a collection of software from AVEVA.
AVEVA’s System Platform acts as Pima County’s “Industrial Operating System” by providing common services such as configuration, deployment, communication, security, data connectivity, people collaboration, and many others. These services enable Pima County to build a single, unified “Plant Model” that logically represents its processes, physical equipment and industrial systems.
The Plant Model also gives essential context to data, greatly assisting with diagnostics and troubleshooting, as well as providing valuable system documentation throughout the system lifecycle.
The Plant Model is unique to System Platform
InTouch integrates with System Platform and provides sophisticated HMI capabilities using common graphics with an object-based engineering approach, and Integrated Development Environment.
These make it easier and faster than ever to create standardized HMI applications and deploy them across all industrial sites, saving up to 70% in development time.
Also, AVEVA was able to take Pima County’s first generation InTouch application and run it on the latest version. AVEVA is the only automation vendor that provides this unsurpassed investment protection.
Situational Awareness Key to Success
Pima County has employed advanced Situational Awareness techniques in its HMI SCADA implementation. This methodology enables personnel to be aware of the processes and systems in their operating environment, understand the information being presented, and acting on that information when needed.
Goal-Oriented Design
The Situational Awareness strategy implemented in Pima County’s AVEVA-based HMI SCADA uses goal-oriented design, effective window structure, color usage, and actionable alarm management.
“A couple of things that were done with our Situational Awareness included keeping it focused, keeping it simple, keeping it easy on the eyes, and keeping things that require your attention to get your attention,” said Larry Sawicki, Control Systems Engineer for Pima County.
The results have been quite dramatic. Operators who previously ignored too many nuisance alarms now take immediate action. Problems are identified and addressed right away before they escalate. “We’ve been able to notice a distinct improvement by operators when things are going wrong and to take suitable response and action,” Sawicki said.
Beyond HMI SCADA
Always on the leading edge of technology, Pima County also uses Mobile Operator Rounds, a sophisticated mobile workforce and decision support system. IntelaTrac collects information from stand-alone assets. Mobile Operator Rounds exception-based, Web reports keep everyone on the team up-to-speed on the current state of plant operations.
“Mobile Operator Rounds allows us to take selected information from the plant that was not previously available in SCADA and push that to SCADA, making the data trendable alongside the information that is already available in the SCADA system,” said Christopher Grant, Program Coordinator at Pima County.
As a mobile workforce and decision support system, Mobile Operator Rounds allows Pima County water technicians to quickly and easily manage operations, both at the plant site and remotely. Mobile Operator Rounds includes configurable software and ruggedised mobile hardware solutions that enable workflow, data collection, and general task management for plant operations, maintenance management, production tracking, and compliance applications.
Its integration with System Platform and Historian provides a comprehensive analysis and reporting solution that accelerates and sustains operational process improvements, a key component of an effective Operations Management System. Mobile Operator Rounds also ensures that best operating and regulatory procedures are followed at all times, and data is collected on non-instrumented plant assets. In addition, critical environmental, health, and safety inspections are performed on schedule, and mobile operators have vital information at their fingertips to operate plant assets in the most effective manner possible.
Pima County Increases Operational Improvements with AVEVA
At the Tres Rios facility, Pima County has achieved 50% increase in operational efficiency and a 10% reduction in energy consumption. “The new SCADA system at Tres Rios has allowed us to double the capacity of the plant while operating with the same number of people we had on staff before the expansion,” said Rod Graupmann, SCADA Manager for Pima County. “That roughly equates to 50% increase in operational efficiency.”