Change Management – The Key To A Successful Digital Transformation Part 3 Blog
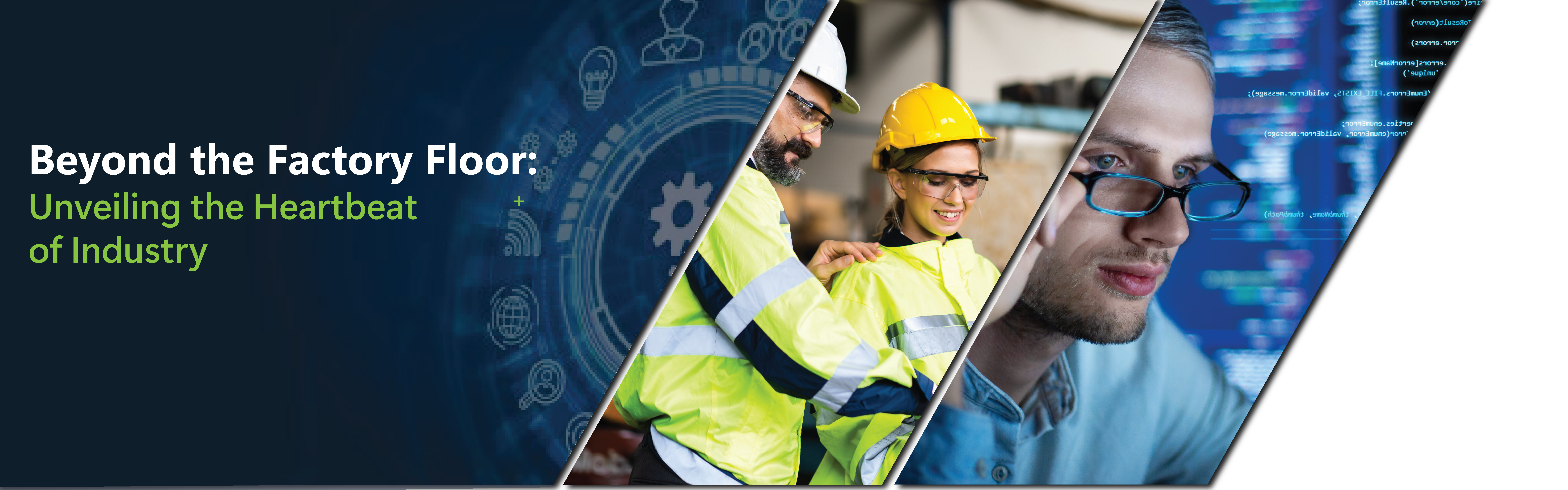
In parts 1 and 2 of this Change Management series, we addressed the classic quality concept of PDCA (Plan-Do-Check-Act) and how it is used during the Planning and Doing stages of change management. In Part 3, we will focus on the “Check” stage. Change management is the skillful management of modifications and advancements within a business or organization. It plays a critical role in achieving a successful digital transformation and emphasizes the significance of effective change management. The process starts from the ground up, highlighting the need for a comprehensive approach.
Our previous discussions explored the vital planning and implementation stages of change management. Now, let’s examine phase 3, the Check stage. During the Check process, assembling the right cross-functional team is essential to minimize unintended consequences as you move forward. Depending on the specifics of the change, the teams involved in planning and implementation may also play a role in the Check stage.
Remember that teamwork is crucial to the planning process. By assembling the right cross-functional team, you can ensure minimal unintended consequences as you proceed.
In the Plan phase, we discussed:
- What would be the problem to correct?
- Who would be affected?
- Where was the change taking place?
- When was the change to be rolled out?
- How would this be implemented?
- And most importantly, why are we attempting this change? Is there a reasonable ROI for all the work put into this?
In the Do phase, we introduced tools to help keep the project organized and productive:
- Project Charter – created and signed off by a member of local leadership, displays members, approximate timeline, and goal of the project with expected outcomes.
- Swimlane Flowchart was created to show the process modifications that need to be enacted. (chart below)
- Action Item list – used to track actions required to keep the Do stage on track and people accountable.
So far, the improvement project has been going well; it is time to discuss the follow-up needed to measure just how well! Successful change management work always includes the Check. In the early stages of change management, Check is essential in ensuring that the Plan and Do fulfill expectations. Check encompasses the three primary legs of an operation: People, Process, and Technology. Checking the status of these three items does not need to be difficult or time-consuming, especially in this early stage. In the early Check stage, a plan for follow-up needs to be created, encompassing the PPT. Parts of the plan need to include verification and follow-up on the items below:
- Production scheduling – does the schedule consider the new segment of production?
- Have training documents been created?
- Have operators been trained in the new way of working?
- Are the operators comfortable and confident in the work?
- Are the machines measuring output correctly and timely?
- Is the performance of the machine at or above specification?
- Get feedback early and often from the lead operators, as they will have insight into how the process is running.
- Follow-up with the Quality department to ensure testing is occurring and specs are being met
- Ensure the Sanitation group is informed of any changes to their routine
- Ensure packaging needs are being met, communicate with floor logistics
All of these above activities are a part of standard work. Standard Work, often referred to as Leader Standard Work (LSW), is the organized manner in which work is performed and applies to all levels of an organization. Integrating the new checks/activities into existing routine activities will help ensure all of the shifts and people are doing things in the same way (whether the working part or the follow-up)
The Check portion will depend on accurate reporting, integral to any manufacturing facility. The Check phase will include reporting to the leadership team and the corporate offices. Accurate data that measures the critical items will assist with tracking how well the project is progressing.
Bottom line – The Check phase of the PDCA process verifies how well the planning and doing stages aligned with the reason for performing this task in the first place! Checking is analogous to sampling your recipe from the oven; you find a recipe and plan it carefully, then make and bake the cake. The Check is trying out your masterpiece and verifying it is as delicious as expected! In Part 4, we will discuss the intricacies of “Act” and see how to modify/improve our “recipe” based on data.
InSource Solutions can help guide you through planning a successful digital transformation to ensure a successful journey. Don’t hesitate to contact us today.
Latest Updates
-
Blog
Operational Technology Support, Reimagined with InCommand
-
Resource
InSource Solutions donates Festo Mechatronics Learning System to Piedmont Technical College to support advanced manufacturing education in South Carolina
-
Event
Dream Report Fundamentals – Live Online
19 Aug - 21 Aug, 2025 -
Event
InSource Innovate 2025
23 Sep - 26 Sep, 2025