Turning Hidden Inefficiencies into Competitive Advantage: Key Insights from Our Braincube Webinar
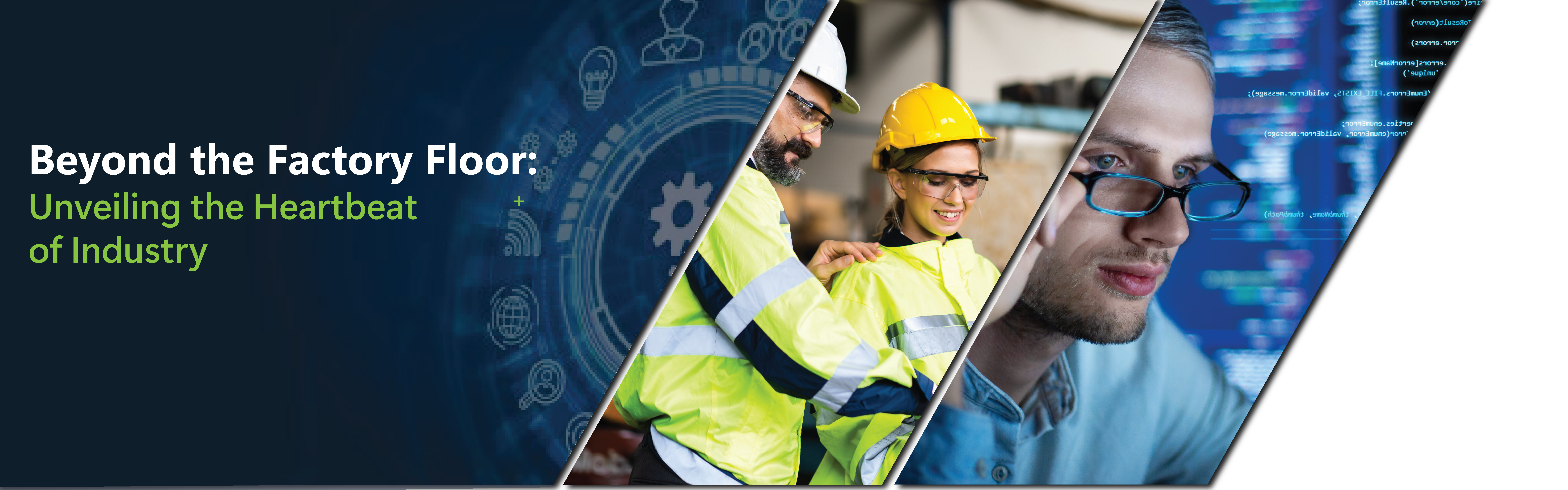
For manufacturing leaders, the mandate is clear: deliver more with less. You’re expected to execute at scale, align operations with business goals, improve productivity, and improve performance that moves the needle on profitability without overhauling your existing systems. That’s where Braincube comes in. Designed to work seamlessly with the platforms you already rely on—like AVEVA MES and the PI System—Braincube helps you get more value from your data faster. It enables teams to identify inefficiencies hiding in plain sight, make smarter decisions on the floor, and connect those decisions directly to enterprise-level outcomes. The result? A clearer path to total productivity, with quick ROI, better alignment across departments, and no capital investment required.
In a recent webinar, Kurt Peterson, Solution Engineer at Braincube, offered a behind-the-scenes look at how manufacturers are moving beyond traditional tools to uncover untapped potential in their operations. He shared how Braincube helps teams go from reactive troubleshooting to proactive optimization, using real-time data and AI to surface insights previously buried in spreadsheets or siloed systems. Whether it’s closing the gap between quality and throughput, reducing waste, or aligning daily decisions with long-term strategy, Kurt demonstrated how Braincube equips teams with the visibility and confidence to make changes that stick—delivering measurable results from the shop floor to the boardroom.
From Fragmented Tools to Total Productivity
Kurt explained that Braincube acts as a Productivity Management System that works alongside your existing systems. It doesn’t replace them—it enhances them.
The goal is simple: give engineers and operators full, end-to-end visibility into their processes so they can identify what’s working, what’s not, and what’s possible.
A drywall plant in Kentucky provided a real-world example. Despite being lean, Six Sigma-trained, and fully equipped with modern tools, they still couldn’t consistently solve quality issues—like voids in boards—that kept cropping up. The problem wasn’t a lack of data. It was the inability to see the whole picture. Braincube gave them that view.
With a digital twin (or “Product Clone”), the team could trace every step of production and identify subtle but critical correlations between upstream variables and downstream outcomes. In the case of the drywall plant, what looked like a problem in the slurry line originated in milling—something they never would’ve caught with their previous tools alone.
The “Square of Hope”
One of the most compelling moments in the webinar came when Kurt introduced the concept of the “Square of Hope.”
At a coffee plant run by OFI, engineers were confident that maintaining quality meant slowing down line speeds. It was a tradeoff they accepted—it was better to run safe than risk waste. However, after analyzing their historical data with Braincube’s CrossRank AI, they uncovered something unexpected: scattered throughout the data were instances where high speed and high quality happened together. These weren’t anomalies—they were missed opportunities. That small cluster of success became their square of hope. It proved that optimal performance wasn’t just possible—it had already been done.
Braincube helped the team pinpoint which process variables made those high-performing runs possible. With that insight, operators could lock in the right conditions and consistently start running at those optimal levels.
What made it even more powerful? They didn’t change equipment. They didn’t invest in new infrastructure. Within weeks, OFI saw a 2% bump in yield. Over time, that grew to a 6.5% improvement and a 25% increase in throughput—all by putting their existing data to smarter use.
Aligning Operations to Business Strategy
Priorities can change overnight. One quarter, it’s all about hitting volume targets. The next, it’s cutting costs or dialing up quality. That kind of shift doesn’t just affect leadership; it also hits the plant floor. Teams need to be able to pivot without missing a beat.
That’s where Braincube comes in. It bridges the gap between high-level business goals and what’s happening in real-time on the line. Whether you’re trying to troubleshoot quality issues, ease production bottlenecks, or keep up with customer demand, Braincube helps teams stay focused, aligned, and ready for whatever comes next.
Watch a short clip of the webinar below or watch the full webinar here!
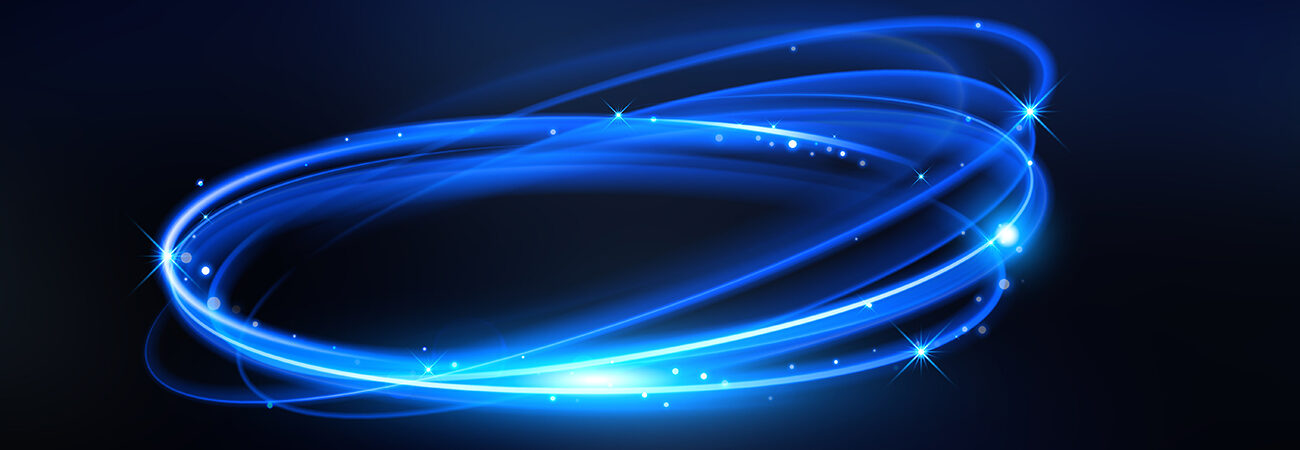
Want To See Braincube in Action?
Watch the entire webinar to dive deeper into the live demo, real customer results, and expert insights that can help you take your operations to the next level.