Mastering Manufacturing: Continuous Improvement Requires Continuous Upskilling
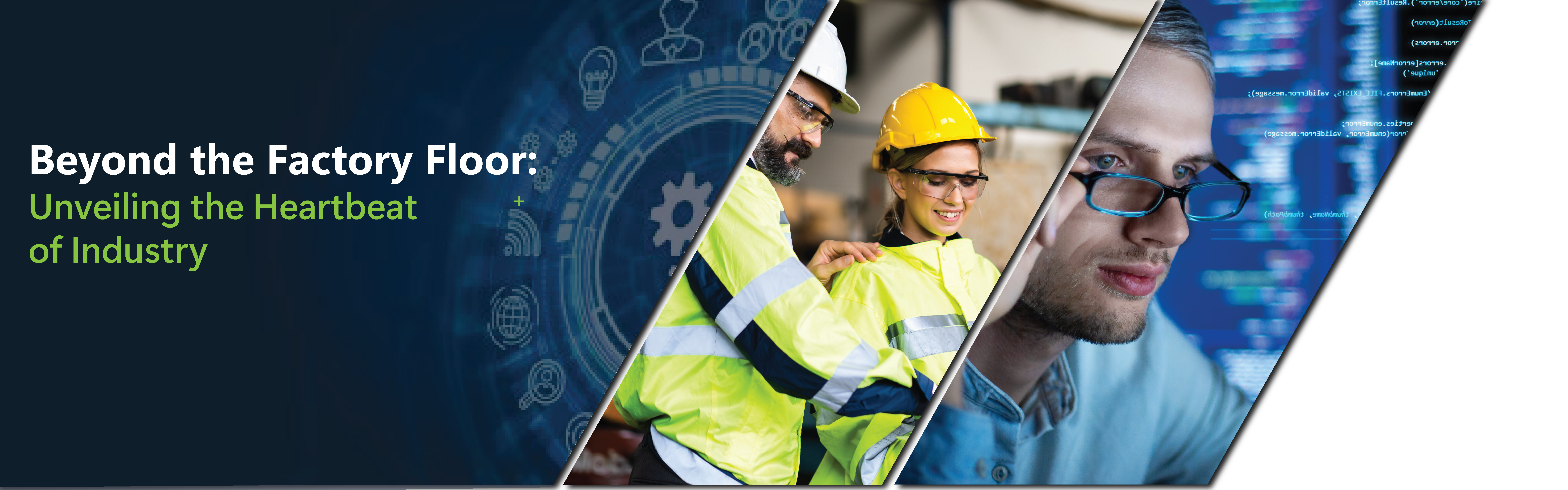
The dynamic nature of industrial operations and the continuous evolution of software stresses the essential need for training your workers. As technology evolves at an unprecedented rate, workers must adapt to new tools, systems, and processes to remain competitive and efficient. With proper training, employees can leverage the full potential of emerging technologies in support of innovation. By investing in training initiatives, companies can ensure that their workforce remains agile, adaptable, and capable of harnessing the latest advancements to drive growth and success in an increasingly dynamic industry landscape.
Today, Manufacturing leaders face a monumental challenge in attracting, onboarding, training, and retaining employees with the technical skills required to keep a modern industrial facility operating. To make things worse, the tech stack underpinning that enterprise continuously evolves to meet ever more stringent security and functional requirements. Add to that the fact there’s always “another new thing” that needs the attention of your smart guys (AI, anyone?). The demands on automation teams never seem to end, and maintaining an entire staff with the capabilities required for success is a challenging endeavor for many plants.
In the National Association of Manufacturers (NAM) Manufacturers’ Outlook Survey—Fourth Quarter 2023, 71% of respondents identified “Attracting and retaining a quality workforce” as a primary business challenge. This has been the highest-ranked business challenge in this survey for 23 of the last 24 quarters and has been in the top four for twelve years running!
You might have heard the analogy that companies often feel like they’re “changing the tires on the bus while the bus is in motion.” For manufacturers, it can feel like “changing the tires on the bus while the bus is in motion, without training or the benefit of the tribal knowledge that left the organization six months ago…”
Technical staffing, in particular, is a multivariate problem with no easy path to success. Clearly, there’s a need for training, but formal training is only one part of a comprehensive skills management program. Do you have a strategy for identifying and prioritizing the most critical skills needs? Do your newer / younger engineers have someone to lean on for practical, real-world, “been there done that” experience? And where will they turn when faced with a problem that exceeds their current skill level?
While we can’t address every skill need an industrial facility might have, InSource has developed the InSider+ program to give you “insider access” to our expert-level resources for automation software products from AVEVA. InSider+ includes these elements:
- Unlimited training: Join any class that’s on our published schedule. Options include in-person, virtual, self-paced, or short video snippets. Take advantage of our Curriculum Coach to help you create a customized training plan that considers your organization’s installed license base and aligns with your business objectives.
- Access to subject matter experts: Because Googling can only get you so far, you’ll get enhanced access to our factory-certified product experts, who will provide a helping hand or another set of eyes. It’s an easy button for your most demanding challenges!
- Community: Because there’s probably someone out there who has already done what you’re trying to do. Take advantage of the opportunity to tap into the collective wisdom of a vibrant user community.
- Members-only content: Who doesn’t love a little VIP treatment? Access code snippets, pre-configured example solutions, sample database queries for popular AVEVA products, and more.
- Trial software: You can’t test with the systems you use in production daily, right? Leverage a pool of flexible credits that allow you to evaluate software in the context of your environment. Test out new functionality for applications you already own, or try something from the AVEVA portfolio you don’t have today. Use this capability to make informed decisions about your digital transformation journey.
In addition to the complex skill improvements that can be achieved by a comprehensive approach to training and team empowerment, there are often other (significant) secondary benefits. When organizations demonstrate a commitment to employee development, there are corresponding improvements in morale, job satisfaction, and retention rates. Focused employee development also fosters a culture of continuous improvement as employees are encouraged to learn new techniques and stay updated with industry advancements.
The skills battle in manufacturing is real. InSider+ is your secret weapon in this battle! Use it to help close the skills gap you have, and watch the “secondary benefits” roll in!
Latest Updates
-
Blog
Operational Technology Support, Reimagined with InCommand
-
Resource
InSource Solutions donates Festo Mechatronics Learning System to Piedmont Technical College to support advanced manufacturing education in South Carolina
-
Event
Dream Report Fundamentals – Live Online
19 Aug - 21 Aug, 2025 -
Event
InSource Innovate 2025
23 Sep - 26 Sep, 2025