The Digital Transformation of Existing Operational Forms
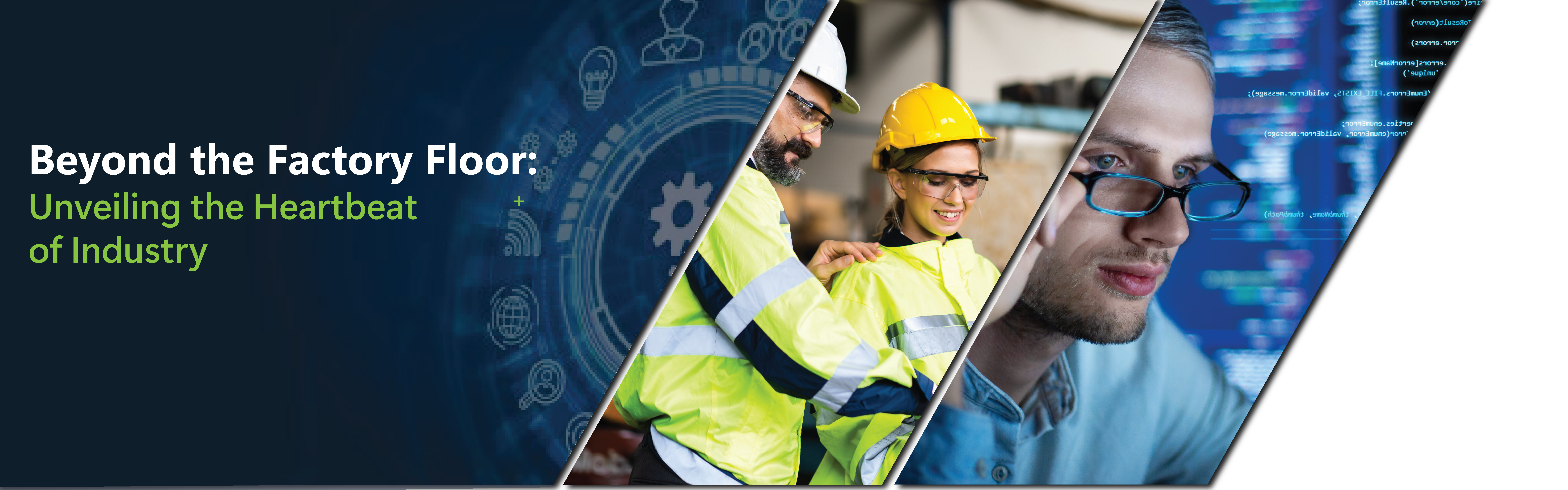
With Industry 4.0 swooping into the Manufacturing Industry, an increased focus by senior management has been to shift operational documents to digital. Since 2020, digital transformation has made the Manufacturing Industry rethink how it can improve its operational goals by effectively and efficiently digitalizing plant floor documentation.
We have seen a shift in recent client engagements and their 2023 operational goals. Senior management has an increased focus and urgency to shift towards transforming existing paper forms to digital, commonly referred to as “paper on glass” initiative. As the rest of their plant floor embraces Industry 4.0, it only makes sense to follow suit regarding everything paper. With these operational shifts, the uncertainty of going digital without disrupting their everyday processes can be challenging. By understanding the overall objectives of the plant floor, digitizing floor paperwork can result in operational benefits if done correctly. By maintaining awareness that digitation of paper documentation is more than just installed and done. This digital process will help a plant evolve and drive continuous improvement year after year.
Operator floor documentation is developed to drive and support consistent operating practices which allow for desirable and repeatable outcomes. Operator and Supervisor documentation is the first to be looked at when transitioning to digital. Operator documentation comprises checklists, downtime documentation, quality control, material variances, safety observations, and more. Checklists, for example, are used at the start of a shift to clean, inspect, and lubricate (CIL), and changeovers. Supervisor documentation is used for floor walks and end-of-shift documentation. Both documentation is used in conjunction with each other, which allows the plant floor to run efficiently and effectively.
These existing paper forms, like the CIL Form, are a great starting point. When transforming them into digital documents, the results often show increased granularity and comprehensiveness of the floor operations. These digital documents capture more information than currently exists on paper forms and can be quickly filed and updated to show data throughout the year. Going digital will also enable the shop floor to communicate data faster to upper management. The shop Operator and Supervisor can also ensure they are simplifying operational workflows. Every part of the process, from making the products to package labeling and sanitizing the equipment used, can now be tightly controlled and ensure the process is recorded and done correctly.
The benefits of digitalizing paper documentation and forms can be seen across departments. Although moving from paper to digital can improve your shop floor’s data and processes, it can lead to potential issues if done incorrectly. This includes negative user experience, data integrity questions, limited data mining capability, and ultimately limited use and adoption. Specific steps can help you avoid these potential issues, like ensuring your current forms are in the order the operational processes are conducted on the shop floor.
Potential issues your shop floor could see:
- The need for flexibility in digital forms: Paper forms allow flexibility in the sequence of activities completed. An operator can jump around the document based on how they physically conduct the actions required for form completion. An electronic form is more rigid and structured. Navigation between specific activities completed and their location on the digitized form might need to be more user-friendly and logical so the operator will be willing to adopt the digital form fully.
- Older manufacturing processes need to be updated: Existing documentation may have been developed under different manufacturing practices and procedures. Equipment and processes captured on paper forms may no longer exist or exist radically different way. A paper form is easy to correct by physically lining sections and adding appropriate commentary. A digital form may require input to every field, whether it is relevant or not.
- The flexibility to add to the digital form: From an engineer’s perspective, more data is always better than less. This can lead to excessive information documentation and add to the users’ burden of completing the form. Often less can be better than more in the digitation process, focusing on required, need-to-know data. The nice-to-know data only adds to the operator’s completion burden and can lead to an overall degradation of the data captured.
A recent example of where more may not be better is the expansion of operator responsibility of continuous improvement documentation. A corporate Continuous Improvement team led the initiative. The operators now have a digital form to complete for minor operational line changes, replacements and adjustments; a root cause analysis form (RCA) for minor line downtime events; and a third Breakdown Defect Review (BDR) form for major downtime events. The downtime RCA and BDR forms are multiple tabs and require significant time for the operators to complete. Floor compliance has been low since the operators still have their primary job responsibilities of running the line. Continues Improvement is significant but additional operator requirements must be integrated into the daily work activities, not just added on. After deployment, this integration process addressed the compliance issue with InSource Solutions guidance, which should have happened before the deployment of the solution.
Digitizing an obsolete / non-functioning form does not support the digitization use case. Existing forms need to be critically assessed for current fitness for use and relevance of information captured. This should be approached holistically with both the capturers and consumers of the data involved in the validation process.
Digitization is the way of the future but should be approached in a structured and systemic way. Having a partner guide you through the digital transformation steps can help ensure a smooth transition. We at InSource Solutions pride ourselves in having the knowledge, experience, and understanding to guide our clients through the successful deployment and adoption of a digital solution, which has led to many successful shop floor digital transformations. Contact us today to learn more about how InSource Solutions can help you with your digital transformation.