Understanding and Applying Overall Equipment Effectiveness (OEE)
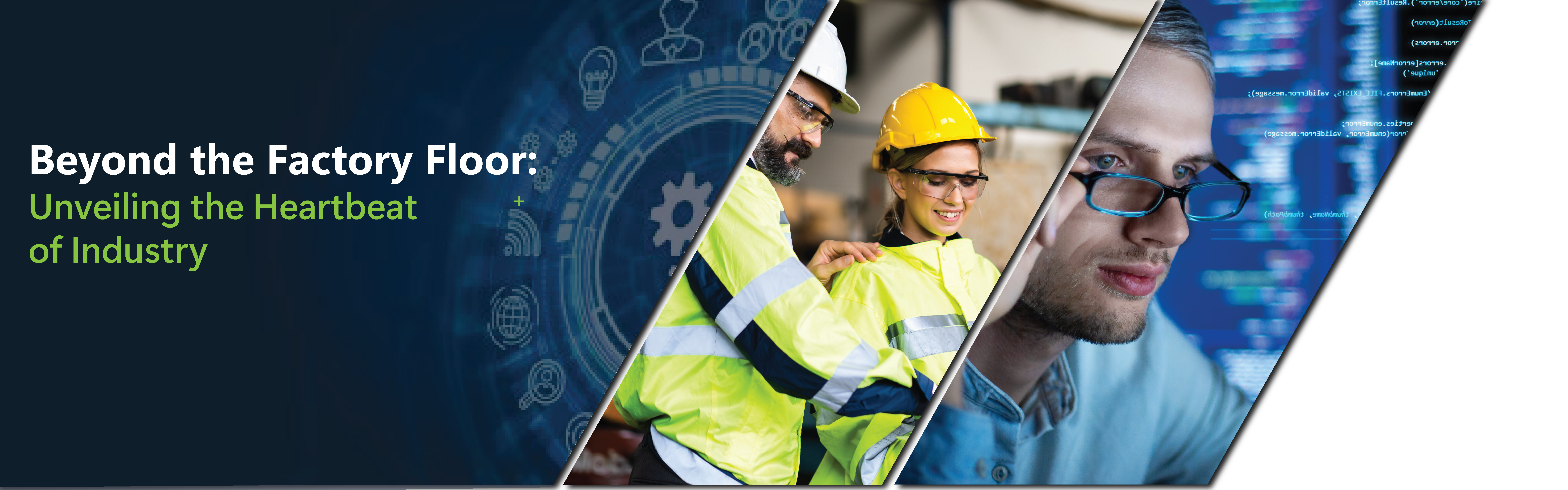
Overall Equipment Effectiveness (OEE) is a standard for measuring operational efficiency in manufacturing. It consists of three components: Availability, Performance, and Quality. By using OEE, manufacturers can identify areas for improvement in their production line. For instance, if the individual components of OEE are improved, the overall OEE score can be increased, enhancing plant performance. In this example, we calculate OEE for a production line during an 8-hour shift.
More and more businesses are adopting to measure themselves using the Overall Equipment Effectiveness (OEE) standard, defined as Machine Availability x Performance x Quality (sellable units as a %). In my various assignments as an operations architect with InSource Solutions, I see many customers utilizing OEE. So, how do you calculate OEE, and how can it be used to help improve plant performance? Let take a look at the example below:
Example: If you have perfect uptime (Availability), your unit-producing machine runs at its engineered rate (Performance), and everything produced is of good Quality (Quality), then the result would be an OEE of 100%. It is helpful for manufacturing to consider these components and their impact on the plant’s overall profitability. Identifying the subpar component is the first step toward correcting the issue(s).
We will focus on defining the role of these three key elements and describing their impact on plant OEE. We will describe the individual components, giving examples of the factors influencing each.
For our examples, we will refer to a production line OEE, meaning we will look at how the overall line has performed during a scheduled 8-hour shift. It is also possible to measure the effectiveness of individual assets comprising the line, but not for these examples.
Availability: Availability is binary: on or off, running or not running. An important learning for OEE is to remember that OEE is measured against scheduled time, not unscheduled time. When a plant measures all time for availability, it is called TEEP Total Equipment Effective Equipment Performance, but that is for another time.
An example of availability is that the scheduled time is 8 hours, but the unit-producing machine only runs 6 hours. Having 6 hours of run time / 8 hours, yields planned a 75% available value. Items such as changeovers during the shift get counted as downtime, and any other unplanned stoppages so that we will have 75% as our availability score. As a formula:
Availability = Planned time – non-running time / Planned time x 100%
8 hours planned – 2 hrs. down / 8 hrs. planned = 75%
Performance – Performance measures how well the line runs compared to the engineered capacity, sometimes referred to as theoretical maximum or Tmax for short. Performance is measured while the line is running; while the line is not running, the line takes an availability hit, not Performance. It’s important to remember that there is no double jeopardy in OEE; it’s either an Availability or Performance problem at any time.
Performance measurement is not binary like availability values. Performance values are measured in units, e.g., pieces per minute, feet per hour, tons per hour, or widgets per second, you get the picture. Performance can range from 1% to 100% theoretical. Performance values cannot exceed 100%. If they do, that indicates your tmax value is too low and needs to be recalculated, or your counter adds “false” units.
Let’s look at an example. Based on our availability example, we have six (6) hours of run time for the calculation. When the line runs, it can produce 60 units an hour. Over a period of six hours, the line could have made 360 units (6 hrs x 60 units). The line only produced 300 units during those six-run hours. Here is our formula.
Performance = Actual units during run time / Planned units x 100%
300 actual units /360 potential units = 83.3%
Quality—The Quality component of OEE considers the percentage of units created that are of good Quality and can be sold. Multiple quality checks are performed to ensure the units pass all of them before being shipped out.
Let’s look at an example. Based on our Performance, the line made 300 units, but after inspection, we found that 40 units were unacceptable. Of 300 units, 260 were still high Quality and could be sold. Here is our formula.
Quality = Good units / Total units x 100%
260 actual units /300 total units = 86.7%
Summary from the example.
OEE – The overall score from our example is:
Availability x Performance x Quality = OEE
(A) 75% x (P) 83.3% x (Q) 86.7% = 54.2%
Bottom line – While the 54.2% OEE is a low number, it is not that far from what we see in plants across America.
Note that the OEE value is directional, but the components tell a deeper story about what is occurring on the production line. OEE is the lagging indicator. You don’t directly correct OEE. You correct the components, and the OEE improves. Every time you correct one of the three components, OEE improves. Individual values allow the management team to direct resources to conquer operational issues. As OEE values improve, the plant can raise the goal to better match current Performance.
For further guidance on OEE and other operational issues, we at InSource are here to assist you in your journey toward improved Performance. Feel free to contact us.