Smart Manufacturing Starts with Execution Discipline — Not Just Tech
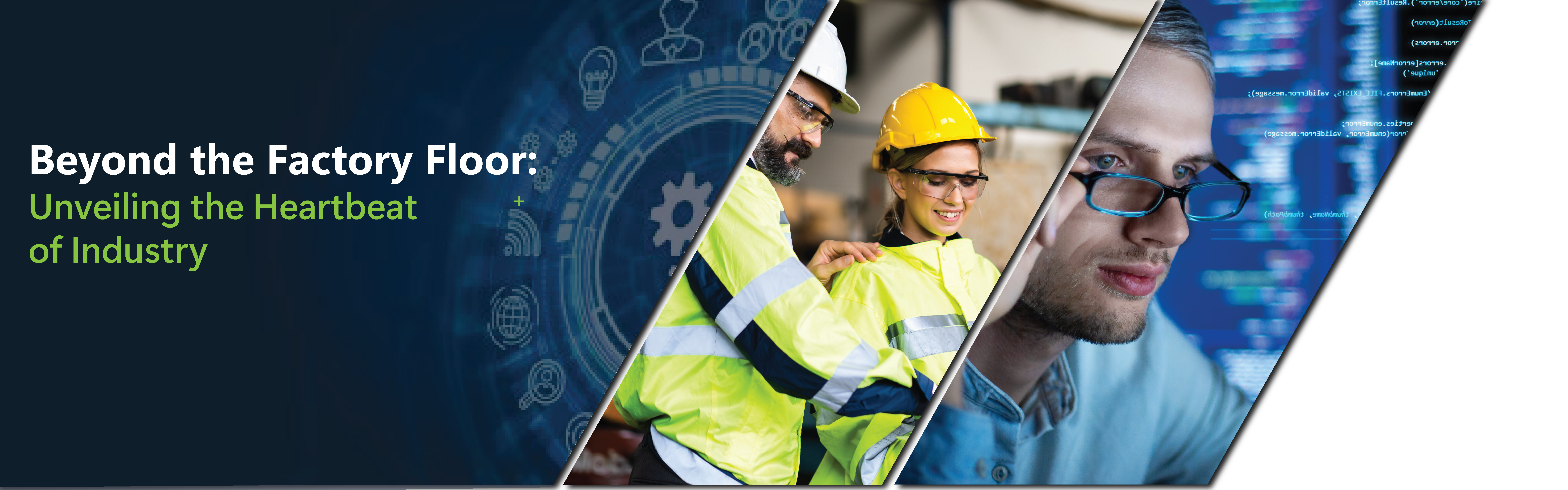
You know that iceberg graphic everyone loves? The one that shows how 90% of the iceberg sits below the surface, hidden and dangerous? Here’s a bold truth: Your manufacturing tech stack might be the Titanic. And unless you’ve got the right operational discipline supporting that shiny MES software, you’re on a collision course.
We recently hosted a webinar with our partners at AVEVA to talk about what makes a smart manufacturing initiative succeed—and spoiler alert: it’s not just about the software. Nick Nicholas, Sree Hamid (both from AVEVA), and our own Jeff Miller dove into what makes MES the heartbeat of smart manufacturing and why the execution layer is where the magic (or mayhem) happens.
MES: Still Misunderstood, Still Mission-Critical
Despite decades in the market, MES (Manufacturing Execution Systems) still has people scratching their heads. What exactly is it? What does it do? Here’s the short version: MES sits right between planning and control. It turns production plans into plant floor action—and captures all the real-time data along the way.
Sree reminded us that MES isn’t just about better scheduling or traceability (though it helps with both). It’s about execution discipline. When done right, it pays off—fast. ROI in under a year fast. And with today’s hybrid cloud options, that timeline is shrinking even more.
But here’s the catch: MES doesn’t work in a vacuum. It needs process clarity, standardization, and buy-in from every corner of your operation. That’s where the rest of the iceberg comes in.
From Garage Band to Philharmonic
Nick walked us through AVEVA’s MES footprint—and introduced a musical metaphor we can’t un-hear.
Think of your shop floor like a band.
- A garage band? Loose coordination, lots of improvising.
- A jazz quartet? There is more structure but room to riff.
- A full-blown orchestra? High-level synchronization and precision.
Your MES implementation needs to match your operational style—and help elevate it. AVEVA’s model-driven, composable MES approach lets you build what works for your plant now and scale it as your performance matures. Whether you’re fine-tuning one line or rolling out to 160 sites like Barry Callebaut did, it’s about choosing your rhythm—and sticking to it.
The Real Work Lives Below the Waterline
Jeff brought it all home with a sharp visual: the iceberg. In digital transformation, technology is just the tip. The rest—the change management, the process redesign, and the people development—determines success or failure.
He shared a stat that stopped us in our tracks:
75% of manufacturing software initiatives fail to deliver meaningful results. Why? Because they try to layer tech on top of outdated ways of working. They skip the hard conversations about the process. They assume people will just “figure it out.”
But transformation doesn’t work that way. Not in manufacturing. Not when your team’s performance depends on seconds, specs, and shifts.
That’s why InSource focuses just as much on the 90% under the surface. We help clients rethink how they plan, execute, and improve—not just how they install software.
MES Is a Journey—Not a Button
Over the course of the webinar, a few things became very clear. First, smart manufacturing isn’t a standalone initiative. It’s part of a broader strategy that spans planning, control, people, and data. Second, success comes from building cross-functional alignment—from standardizing your approach across plants to empowering your people to act on real-time insights. And third, you can’t fake execution discipline. It takes effort, vision, and the right partners.
Whether you’re rolling out MES across six sites or piloting a new process in one, the road to transformation starts with asking the right question—not just “What software should we buy?” but “What are we trying to achieve?”
If you’re ready to move beyond the buzzwords and into tangible results, we’re here to help. Contact us today.
Watch The Full Webinar
Watch the full webinar to explore how AVEVA MES powers smart manufacturing—and what it really takes to succeed.