Food and Beverage
Food and beverage manufacturers constantly face challenges brought on by furious competition and slim margins. To stay profitable, leading companies are always exploring solutions to lower costs and drive operational efficiency across their operations. For over 25 years, InSource has helped clients address the top 5 issues below:
What To Improve | What To Measure | What Results to Expect |
---|---|---|
Filling & Packaging Area Efficiency | Line Efficiency Downtime | 10% Increase 10-25% Reduction |
Workforce Optimization | Product Labour Manual Reporting | 30-50% Increase in Labour Efficiency |
Improved Asset Reliability | Overall Maintenance Cost Maintenance Labour Efficiency Unplanned Downtime | 30% Reduction 25% Increase 25% Reduction |
Material Loss & Water Reduction | Raw Material Waste | 10-25% Reduction |
Energy & Water Use Efficiency | Electricity Water Fossil Fuel Chemical Waste | 10-25% Reduction in Consumption Costs |
AVEVA MES Software
Maximize profitability, flexibility, quality, and compliance in manufacturing by digitally managing the rules and information for all operational activities and plant events in real-time.
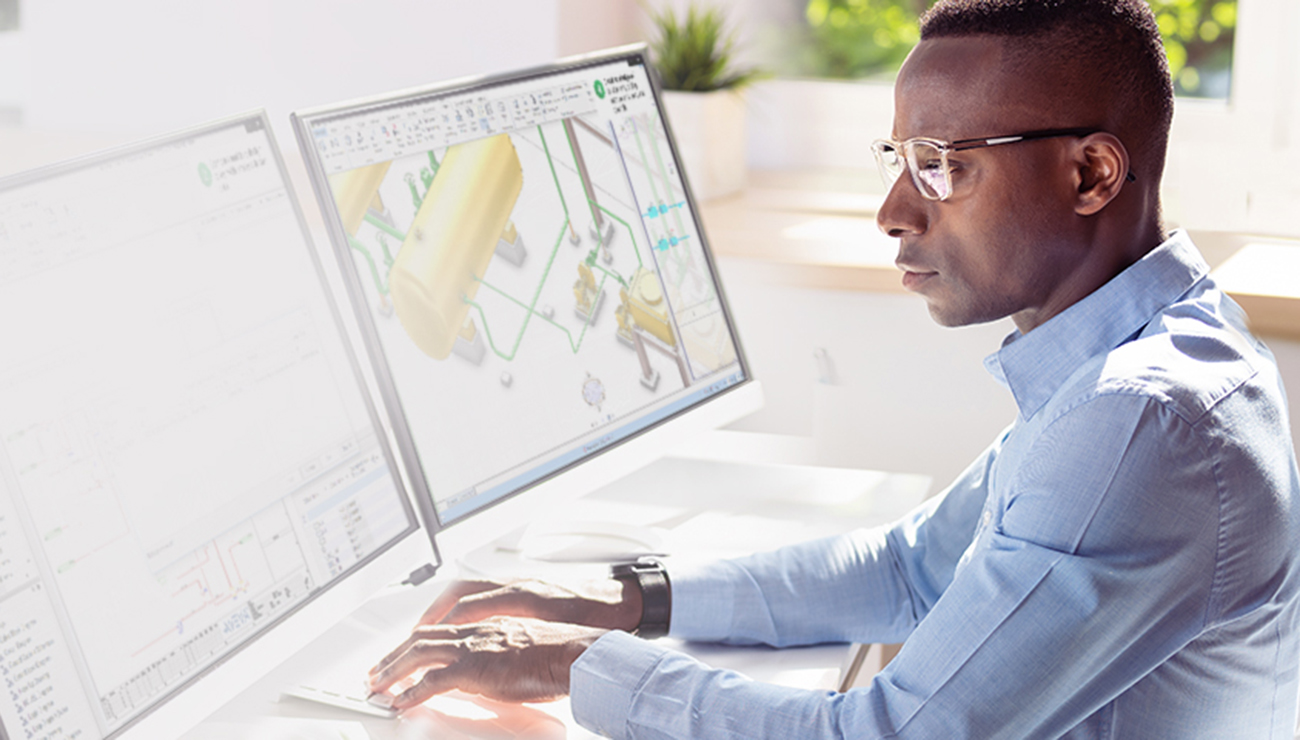
Filling and Packaging Area Efficiency
Commonly, our food & beverage manufacturing clients to ask, why aren’t my packaging lines performing to their design capacities? Specifically:
- What equipment areas are causing downtime?
- What are the root causes of those downtimes?
- What choices are operators making that lead to downtime?
Armed with the answers to these questions, our clients are making better decisions to improve performance and profitability.
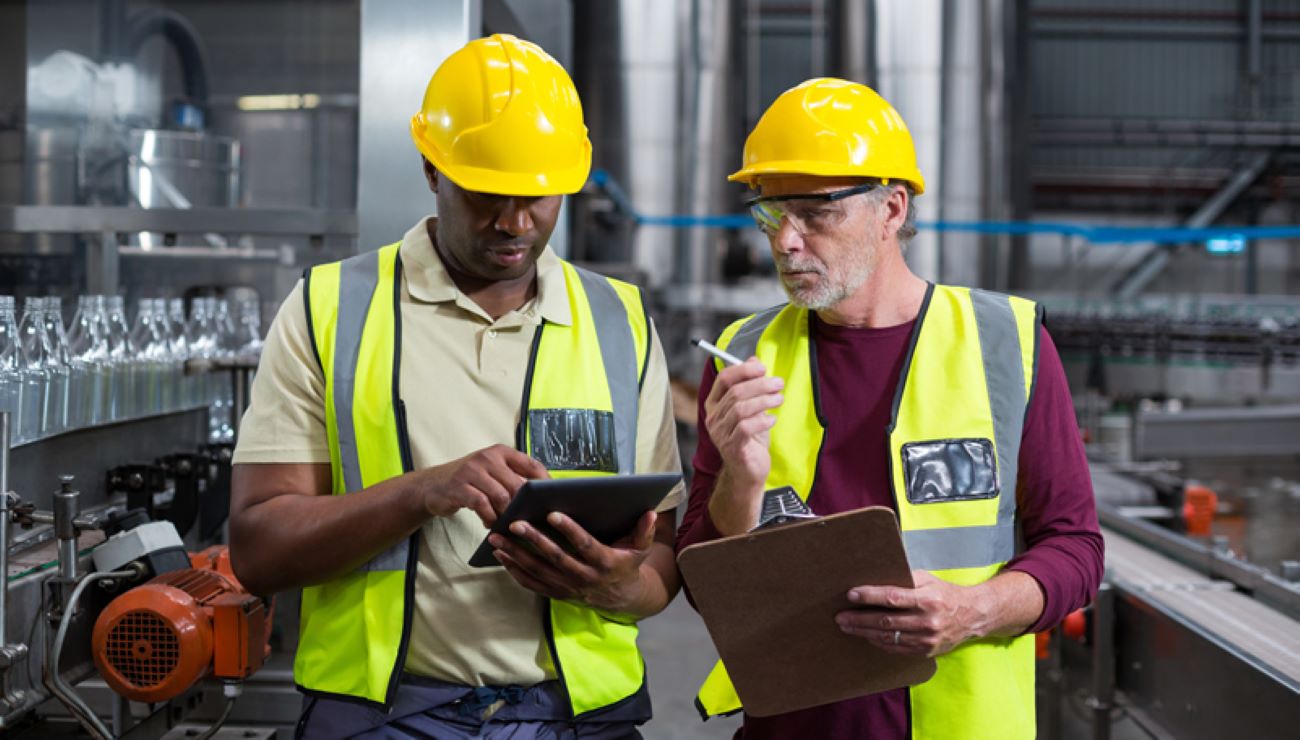
Workforce Optimization
Industrial research has shown the importance of implementing structure with shift handovers in the form of structured logs and checklists. However, an estimated 80 percent of the world’s food & beverage operations still lack a structured approach to shift handovers and use paper logbooks to record critical information. This lack of structure dramatically increases the likelihood for missing critical information and misunderstandings occurring. These misunderstandings and missed information can sometimes have disastrous results. InSource has been leading the way, in helping manufacturers improve shift handovers and optimizing workforce routines.
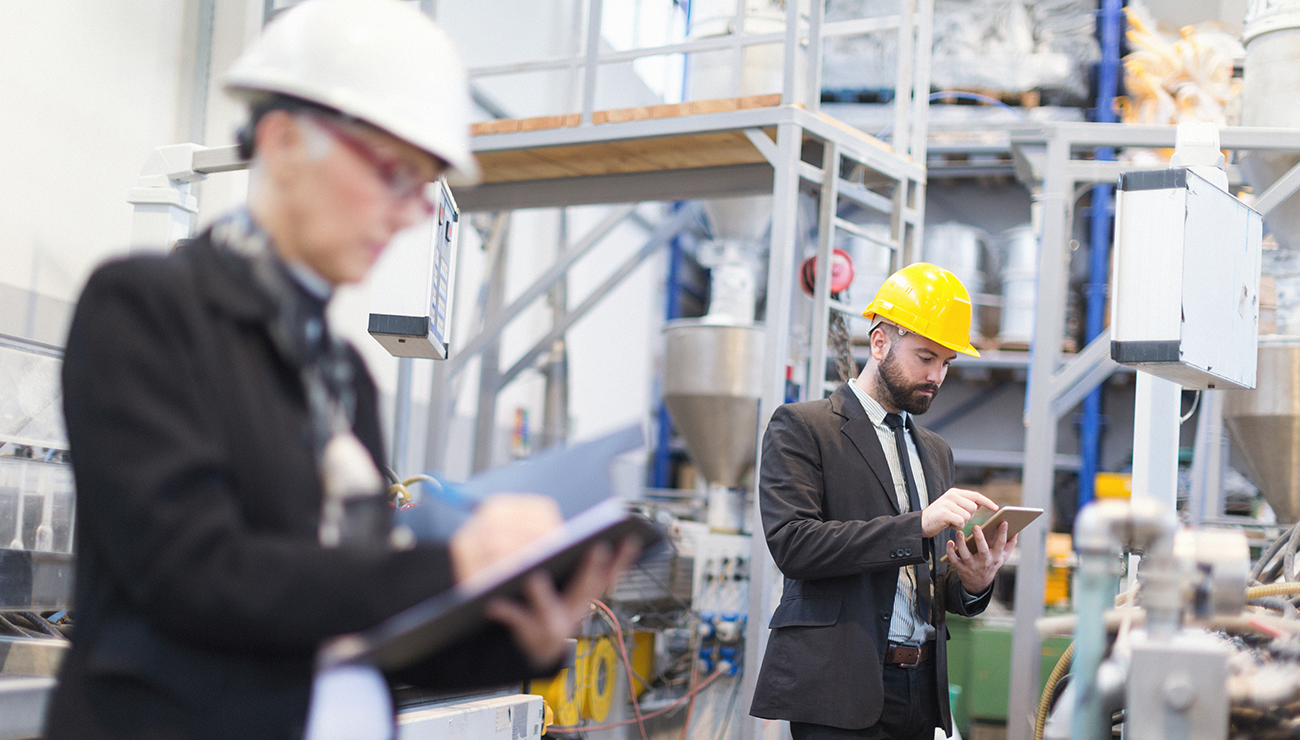
Improved Asset Reliability
Asset Performance Management (APM) helps food and beverage manufacturers improve overall equipment effectiveness (OEE), through improved asset availability. Improving asset reliability is one of the key areas where our clients expect to increase overall profitability. Improved performance means there will be fewer unplanned machine starts stops and better adherence to schedule. This means that quality issues from stop/start cycles are minimized, and “on time, in full” deliveries are maintained. See below for ideas on developing an APM strategy and using sensor data and the underlying conditions they communicate to reduce your unplanned downtime.
Consumer Products
Explore Digital Transformation Solutions in Consumer Products
Case Studies
Get Started with InSource Today
Take the first step in increased productivity and profitability.